|
|
Author
|
Topic: NASA's Artemis I mission (Orion/SLS)
|
Robert Pearlman Editor Posts: 51606 From: Houston, TX Registered: Nov 1999
|
posted 07-09-2013 08:16 AM
NASA release First mission of Space Launch System with OrionManagers in NASA's Human Exploration and Operations Mission Directorate have initiated a formal request to change the mission plan for the agency's first flight of the Space Launch System (SLS), Exploration Mission (EM) 1 in 2017. The flight will carry an uncrewed Orion spacecraft to a deep retrograde orbit near the moon, a stable orbit in the Earth-moon system. The 25-day mission will send Orion more than 40,000 miles beyond the moon and allow engineers to evaluate the performance of SLS and assess the systems designed to support a crew in Orion before the capsule begins carrying astronauts. The previous plan for the first test flight of the SLS heavy-lift launch vehicle was to send Orion on a 10 day mission to high-lunar orbit to evaluate the fully integrated Orion and SLS system. "We sent Apollo around the moon before we landed on it and tested the space shuttle's landing performance before it ever returned from space." said Dan Dumbacher, NASA's deputy associate administrator for exploration systems development. "We've always planned for EM-1 to serve as the first test of SLS and Orion together and as a critical step in preparing for crewed flights. This change still gives us that opportunity and also gives us a chance to test operations planning." The request will be reviewed later this summer by a range of other NASA officials. Across the U.S., engineers at NASA and its contractors are making progress to develop and test Orion and SLS. Orion will first launch on a test flight in September 2014. A United Launch Alliance Delta IV Heavy rocket will send the spacecraft to an altitude of 3,600 miles above Earth's surface. It will reenter the atmosphere at speeds of about 20,000 mph and endure temperatures of 4,000 degrees Fahrenheit. The test flight is designed to evaluate the performance of Orion's heatshield and other systems. The SLS program currently is undergoing an extensive review process to ensure that every element of the launch vehicle can be successfully integrated. The review process, called the Preliminary Design Review, is scheduled for completion later this summer. SLS will be NASA's most capable rocket ever and enable missions to new destinations in the solar system. |
Robert Pearlman Editor Posts: 51606 From: Houston, TX Registered: Nov 1999
|
posted 05-13-2015 03:48 PM
Lockheed Martin release Orion Test Lab Mockup for Next Flight FinishedThe construction of an Orion crew module and crew module adapter full-scale mockup has been completed at the Lockheed Martin Littleton, Colorado facility. 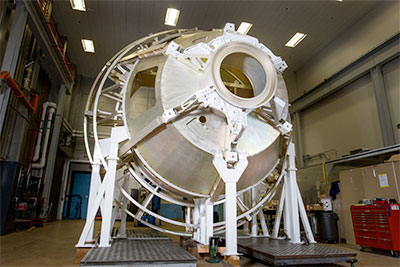 This mockup was transferred to the Orion Test Lab (OTL) on May 13, 2015 where engineers will configure it with the exact harnessing, electrical power, sensors, avionics and flight software needed to support Exploration Mission-1 (EM-1). Orion's team of engineers will use the mockup to verify the configuration of these vehicle components for EM-1 which ultimately saves assembly time and reduces risk. The mockup will then be connected to hardware emulations of the full EM-1 stack (Orion crew module, European Service Module, second stage booster, and the Space Launch System) as well as ground support equipment. Once it's connected, the team will simulate and test every aspect of the EM-1 mission from launch to splash down. |
Robert Pearlman Editor Posts: 51606 From: Houston, TX Registered: Nov 1999
|
posted 09-08-2015 04:31 PM
NASA release First Pieces of NASA's Orion for Next Mission Come Together at MichoudNASA is another small step closer to sending astronauts on a journey to Mars. On Saturday, engineers at the agency's Michoud Assembly Facility in New Orleans welded together the first two segments of the Orion crew module that will fly atop NASA's Space Launch System (SLS) rocket on a mission beyond the far side of the moon. 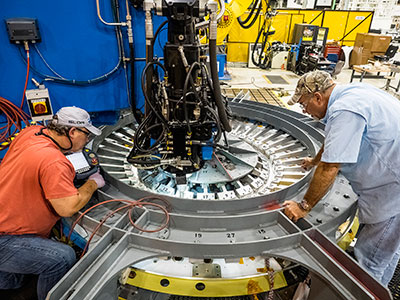 Above: Lockheed Martin Engineers at NASA's Michoud Assembly Facility in New Orleans, Louisiana, perform the first weld on the Orion pressure vessel for Exploration Mission 1. (NASA/Radislav Sinyak) "Every day, teams around the country are moving at full speed to get ready for Exploration Mission-1 (EM-1), when we'll flight test Orion and SLS together in the proving ground of space, far away from the safety of Earth," said Bill Hill, deputy associate administrator for Exploration Systems Development at NASA Headquarters in Washington. "We're progressing toward eventually sending astronauts deep into space." The primary structure of Orion's crew module is made of seven large aluminum pieces that must be welded together in detailed fashion. The first weld connects the tunnel to the forward bulkhead, which is at the top of the spacecraft and houses many of Orion's critical systems, such as the parachutes that deploy during reentry. Orion's tunnel, with a docking hatch, will allow crews to move between the crew module and other spacecraft. "Each of Orion's systems and subsystems is assembled or integrated onto the primary structure, so starting to weld the underlying elements together is a critical first manufacturing step," said Mark Geyer, Orion Program manager. "The team has done tremendous work to get to this point and to ensure we have a sound building block for the rest of Orion's systems." Engineers have undertaken a meticulous process to prepare for welding. They have cleaned the segments, coated them with a protective chemical and primed them. They then outfitted each element with strain gauges and wiring to monitor the metal during the fabrication process. Prior to beginning work on the pieces destined for space, technicians practiced their process, refined their techniques and ensured proper tooling configurations by welding together a pathfinder, a full-scale version of the current spacecraft design. NASA's prime contractor for the spacecraft, Lockheed Martin, is doing the production of the crew module at Michoud. 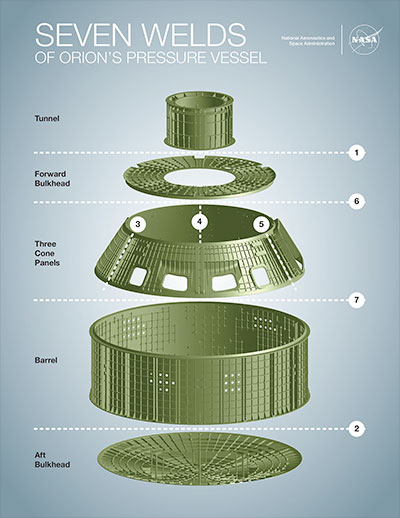 Through collaborations across design and manufacturing, teams have been able to reduce the number of welds for the crew module by more than half since the first test version of Orion's primary structure was constructed and flown on the Exploration Flight Test-1 last December. The Exploration Mission-1 structure will include just seven main welds, plus several smaller welds for start and stop holes left by welding tools. Fewer welds will result in a lighter spacecraft. During the coming months as other pieces of Orion's primary structure arrive at Michoud from machine houses across the country, engineers will inspect and evaluate them to ensure they meet precise design requirements before welding. Once complete, the structure will be shipped to NASA's Kennedy Space Center in Florida where it will be assembled with the other elements of the spacecraft, integrated with SLS and processed before launch. |
Robert Pearlman Editor Posts: 51606 From: Houston, TX Registered: Nov 1999
|
posted 01-19-2016 11:03 AM
NASA release Engineers mark completion of Orion's pressure vesselNASA's Orion spacecraft is another step closer to launching on its first mission to deep space atop the agency's Space Launch System (SLS) rocket. On Jan. 13, technicians at Michoud Assembly Facility in New Orleans finished welding together the primary structure of the Orion spacecraft destined for deep space, marking another important step on the journey to Mars. 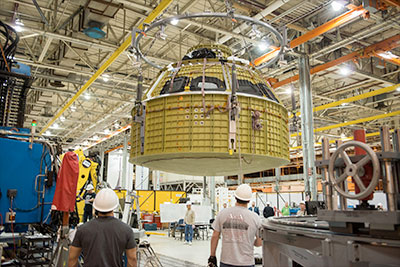 "We've started off the year with an key step in our process to get ready for Exploration Mission-1, when together Orion and SLS will travel farther than a spacecraft built for humans has ever traveled," said Mike Sarafin, Exploration Mission-1 manager at NASA Headquarters in Washington. "This brings us closer to our goal of testing our deep space exploration systems in the proving ground of lunar space before we begin sending astronauts days to weeks from Earth." Welding Orion's seven large aluminum pieces, which began in September 2015, involved a meticulous process. Engineers prepared and outfitted each element with strain gauges and wiring to monitor the metal during the process. The pieces were joined using a state-of-the-art process called friction-stir welding, which produces incredibly strong bonds by transforming metals from a solid into a plastic-like state, and then using a rotating pin tool to soften, stir and forge a bond between two metal components to form a uniform welded joint, a vital requirement of next-generation space hardware. "The team at Michoud has worked incredibly hard produce a lightweight, yet incredibly durable Orion structure ready for its mission thousands of miles beyond the moon," said Mark Kirasich, Orion program manager. "The work to get us to this point has been essential. Orion's pressure vessel is the foundation on which all of the spacecraft's systems and subsystems are going to be built and integrated." 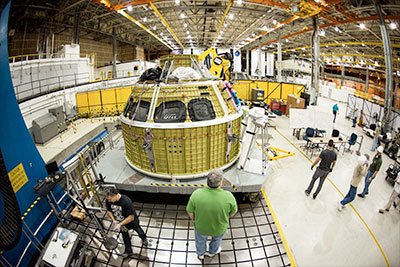 The pressure vessel provides a sealed environment for astronaut life support in future human-rated crew modules. After final checkouts, technicians will prepare the pressure vessel for shipment to NASA's Kennedy Space Center in Florida in the agency's Super Guppy aircraft. At Kennedy, it will undergo several tests to ensure the structure is sound before being integrated with other elements of the spacecraft. The uncrewed Exploration Mission-1 will pave the way for future missions with astronauts. During the flight, in which SLS and Orion will launch from NASA's modernized spaceport at Kennedy, the spacecraft will venture to a distant retrograde orbit around the moon. This first exploration mission will allow NASA to use the lunar vicinity as a proving ground to test technologies farther from Earth, and demonstrate it can get to a stable orbit near the moon in order to support sending humans to deep space. |
Robert Pearlman Editor Posts: 51606 From: Houston, TX Registered: Nov 1999
|
posted 02-03-2016 10:30 AM
Lockheed Martin release New and Improved Orion Crew Module Arrives at Kennedy Space CenterMilestone Marks First Major Delivery of Exploration Mission-1 Flight Hardware The Lockheed Martin and NASA Orion team has secured the 2,700 lb. Exploration Mission-1 (EM-1) Orion crew module into its structural assembly tool, also known as the "birdcage." The crew module is the living quarters for astronauts and the backbone for many of Orion's systems such as propulsion, avionics and parachutes. 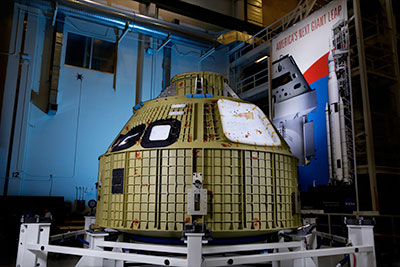 Above: The Orion spacecraft's crew module has been safely secured into its structural assembly tool in the Operations & Checkout Facility. "The structure shown here is 500 pounds lighter than its Exploration Flight Test-1 (EFT-1) counterpart," said Mike Hawes, Lockheed Martin Orion vice president and program manager. "Once the final structural components such as longerons, bolts and brackets are added, total crew module structural weight savings from EFT-1 to EM-1 will total 700 pounds." From experience gained by building test articles, building and flying EFT-1, and now building the EM-1 crew module, the Lockheed Martin team is learning how to shed weight, reduce costs and simplify the manufacturing process – all in an effort to improve the production time and cost of future Orions. "Our very talented team in Louisiana has manufactured a great product and now they have passed the baton to Florida," said Hawes. "This is where we assemble, test and launch, and the fun really begins." 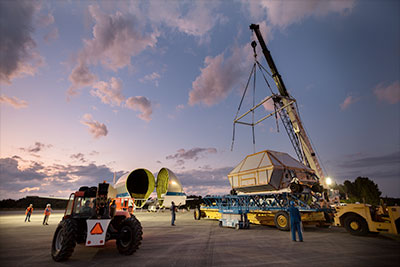 Above: On February 1, NASA's Super Guppy airplane transported the Orion crew module from Michoud Assembly Facility to Kennedy Space Center. At Kennedy Space Center, the crew module will undergo several tests to ensure the structure is perfectly sound before being integrated with other elements of the spacecraft. First it will undergo proof-pressure testing where the structural welds are stress tested to confirm it can withstand the environments it will experience in space. The team will then use phased array technology to inspect the welds to make sure there are no defects. Additional structural tests will follow including proof-pressure testing of the fluid system welds and subsequent x-ray inspections. Once the crew module passes those tests it will undergo final assembly, integration and entire vehicle testing in order to prepare for EM-1, when Orion is launched atop NASA's Space Launch System (SLS) for the first time. The test flight will send Orion into lunar distant retrograde orbit – a wide orbit around the moon that is farther from Earth than any human-rated spacecraft has ever traveled. The mission will last about three weeks and will certify the design and safety of Orion and SLS for future human-rated exploration missions. |
Robert Pearlman Editor Posts: 51606 From: Houston, TX Registered: Nov 1999
|
posted 05-11-2016 12:27 PM
Lockheed Martin release Orion Exploration Mission-1 Crew Module Pressure TestedSpacecraft Approved for Assembly of Secondary Structures The Lockheed Martin (NYSE: LMT) and NASA Orion team has successfully proof-pressure tested the Orion spacecraft's Exploration Mission-1 (EM-1) crew module. The crew module is the living quarters for astronauts and the backbone for many of Orion's systems such as propulsion, avionics and parachutes. 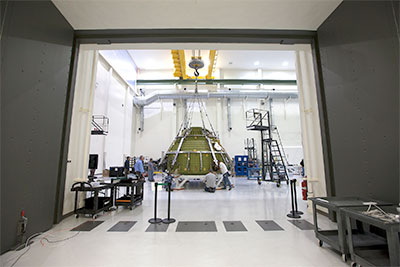 In order to certify the structural integrity of the crew module it was outfitted with approximately 850 instruments and subjected to 1.25 times the maximum pressure the capsule is expected to experience during its deep space missions. That means about 20 pounds per square inch of pressure was distributed over the entire inner surface of the spacecraft trying to burst it from within. As a next step, the team will use phased array technology to inspect all of the spacecraft's welds in order to ensure there are no defects. Once the primary structure of the crew module has been verified, the team will begin the installation of secondary structures such as tubes, tanks and thrusters. Once those pieces are in place, the crew module will be moved into the clean room and the propulsion and environmental control and life support systems will be installed. "Our experience building and flying Exploration Flight Test-1 has allowed us to improve the build and test process for the EM-1 crew module," said Mike Hawes, Lockheed Martin Orion vice president and program manager. "Across the program we are establishing efficiencies that will decrease the production time and cost of future Orion spacecraft." |
Robert Pearlman Editor Posts: 51606 From: Houston, TX Registered: Nov 1999
|
posted 07-29-2016 11:44 AM
NASA release Tile Bonding Begins for Orion's First Mission Atop Space Launch System RocketA crucial part of preparing NASA's next Orion spacecraft for flight now is underway. Technicians recently began the process of bonding thermal protection system (TPS) tiles to panels that will be installed on Orion. The tiles will protect the spacecraft from the searing heat of re-entry when it returns from deep space missions. 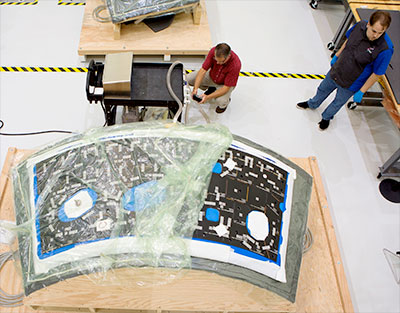 Above: In the Neil Armstrong Operations and Checkout Building at NASA's Kennedy Space Center, technicians have begun bonding thermal protection system tiles to the nine panels the will cover the Orion crew module for the agency's first unpiloted flight test with the Space Launch System (SLS) on the agency's Journey to Mars. The first integrated mission of NASA's Space Launch System (SLS) rocket with Orion, Exploration Mission 1, or EM-1, will lift off from Launch Complex 39B at NASA's Kennedy Space Center in Florida. On the mission, the spacecraft will venture 40,000 miles beyond the orbit of the moon, farther than any spacecraft built for humans has ever traveled, testing the systems needed for the agency's journey to Mars. The mission will conclude with Orion re-entering through the Earth's atmosphere at 25,000 mph, generating heat at about 5,000 degrees Fahrenheit. According to Joy Huff, a thermal protection system engineer in the Materials Science Branch of Kennedy Engineering, Orion's back shell panels and forward bay cover, which helps protect the spacecraft during re-entry, will be protected by silica tiles similar to those used for more than 30 years on the space shuttle. "The seven to eight technicians and two quality inspectors with Arctic Slope Research Corp. doing the work are veterans of bonding tiles to the shuttle orbiters." she said. "The tiles are manufactured here in Kennedy's Thermal Protection System Facility." Denver-based Lockheed Martin Space Systems Co. is the prime contractor for the Orion spacecraft. The company provides digital, computer-aided design information that defines the size and shape of each tile. At Kennedy's TPSF, that information is used to manufacture the tiles. A 3-D camera then scans the as-built shape for comparison to the design information. This ensures that the manufactured tile meets the design requirements before it is placed on one of nine tile panels or the forward bay cover. The bonding process began in July and will take several months. The work is taking place in the high bay of the Neil Armstrong Operations and Checkout Building where assembly of the Orion crew module's pressure vessel, or underlying structure, has been taking place since it arrived at the Florida spaceport in February. Orion will need about 1,300 tiles to protect it. On average, the tiles are 8-inches by 8-inches and many are standard in size allowing them to have the same dimensions with the same part number. "Some tiles on Orion are a unique design to fit around windows, thrusters and antennas," Huff said. Huff noted that Orion tiles incorporate a stronger coating called "toughened uni-piece fibrous insulation," or TUFI coating, which was used toward the end of the Space Shuttle Program. "The 'tougher' tiles are important to Orion as they will help limit damage during ground processing and by debris in orbit," Huff said. Once the tile bonding is complete, the nine panels and forward bay cover will be installed on the crew module after it is mated to its service module. "For EM-1, the back shell panels will have a different look than Orion's first test flight," said Huff. Orion's inaugural mission, known as Exploration Flight Test-1, or EFT-1, was flown on Dec. 5, 2014. On that flight, the tiles gave the crew module a black look. "For EM-1, we will place an aluminized coating over the tiles, giving it a shiny silver look," she said. 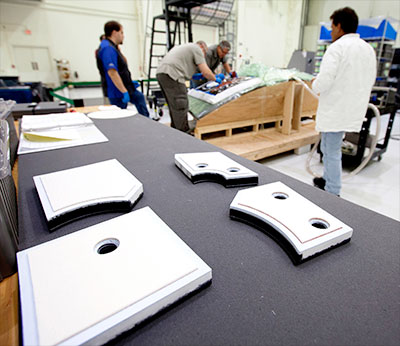 Above: Orion requires about 1,300 tiles. Many of the Orion tiles are standard, except for those which fit around windows, thrusters or antennae. Following deep-space missions, Orion will make a comet-like re-entry through Earth's atmosphere, protected by the tiles and the largest and most advanced heat shield ever constructed. The spacecraft then will splashdown in the ocean. "The fact that Orion lands in the ocean, requires we replace the tiles after each mission," Huff said. "The tiles are waterproofed to protect them from fresh water, such as rain. But during re-entry the waterproofing material burns out of the tiles so they do absorb salt water while in the ocean and that adds contaminants that would make their reuse impossible." Installing TPS tiles will be a part of preparation for each mission. The work taking place now will help perfect the process. For EM-1, Orion will travel well beyond the moon for about three weeks, collecting data and allowing mission controllers to assess the performance of the spacecraft. "We're looking forward to EM-1," Huff said. "SLS is the largest rocket ever built. It will help confirm we're doing things the right way on Orion, and we'll be another step closer to Mars." |
Robert Pearlman Editor Posts: 51606 From: Houston, TX Registered: Nov 1999
|
posted 08-25-2016 07:19 PM
Lockheed Martin release Heat Shield Designed to Protect Orion Ships to Kennedy Space CenterThe Orion team at Lockheed Martin's Space Systems Company facility outside of Denver recently completed and shipped the heat shield structure for the Exploration Mission-1 (EM-1) spacecraft. At 16.5 feet in diameter, the heat shield for Orion Exploration Flight Test-1 (EFT-1) was the largest composite heat shield ever built. And now, the team has completed the second. 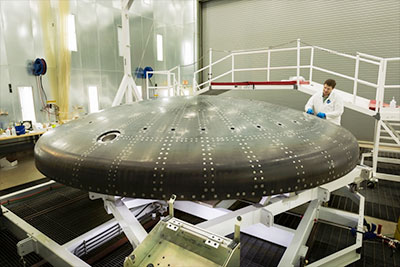 Among members of the heat shield manufacturing team, enthusiasm and excitement was high. "Working on the Orion heat shields is my favorite project," said James Beffel, a machinist in the Prototype Development Center where the heat shield and other spacecraft structures are machined. "It's not just the size and complexity, but the Orion mission as a whole. It's an emotional motivator to know that I helped build a critical part of these missions that are redefining human spaceflight." "I've only been with Lockheed Martin for about a year-and-a-half, and this is my first build of this magnitude in size and logistics," said Matt Rieck, a manufacturing engineer. "I came from the missile defense world, so this is the first thing I've worked on that I want to see fly." 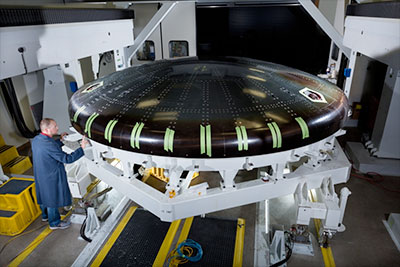 Planning for a heat shield build of this complexity can begin up to a year in advance of production. Matt is already working on capturing lessons learned and beginning to coordinate the logistics for a static test article build, which will be the model for the Exploration Mission-2 heat shield. Over the next six months, the team at Kennedy Space Center will install Avcoat blocks, flight instrumentation and multi-layer insulation onto the heat shield. Once those steps are complete, the new, lighter-weight heat shield be installed onto Orion's crew module — one of the program's major assembly milestones ahead of flight. Orion's heat shield will protect the spacecraft during the entire EM-1 mission which includes about three weeks in deep space, over 4500°F re-entry temperatures and a safe splashdown in the ocean. |
Robert Pearlman Editor Posts: 51606 From: Houston, TX Registered: Nov 1999
|
posted 02-17-2017 12:00 PM
Boeing release First Flight Hardware Ships to Cape CanaveralWorkers at United Launch Alliance (ULA) in Decatur, Ala., will soon ship to Cape Canaveral the Boeing and ULA built second stage propulsion element that will fly on NASA's Space Launch System's first flight in 2018. 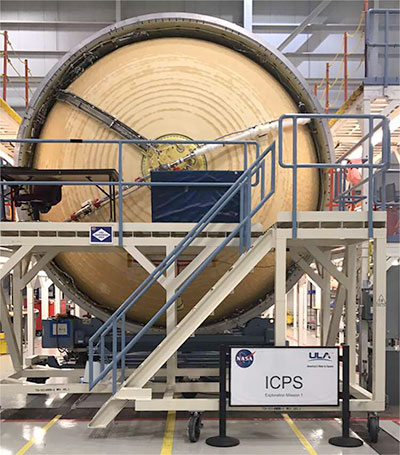 Called the Interim Cryogenic Propulsion Stage (ICPS), it is a modified Delta IV second stage, designed by Boeing to propel Orion beyond Earth's orbit on the first integrated flight of SLS and Orion. This test flight of SLS will lift the Orion capsule beyond Earth. The ICPS will provide the Trans Lunar Injection (TLI) burn to send Orion and the service module on its way to the moon. Concurrently, Boeing is working on the second stage for the next SLS mission, EM-2, which will carry crew and cargo farther into deep space with a more powerful Exploration Upper Stage. |
Robert Pearlman Editor Posts: 51606 From: Houston, TX Registered: Nov 1999
|
posted 08-08-2017 08:03 PM
NASA release Space Launch System Solid Rocket Boosters 'on Target' for First FlightProduction of the five-segment powerhouse motors for the Space Launch System (SLS) solid rocket boosters is on target at prime contractor Orbital ATK's facilities in Utah, with 10 motor segments cast with propellant and four of those segments complete. Following propellant casting, the finished segments were evaluated using non-destructive techniques, such as x-ray, to ensure they met quality standards, and the exterior cases were painted white with black-and-white photogrammetric markings. All motor segments will ultimately be shipped to Kennedy Space Center, where they will be integrated with forward and aft booster structures and then with the SLS core stage. The markings on the outside of the complete boosters look like black-and-white checkerboards and serve as "targets" for cameras located in strategic locations on and around the vehicle and will be used for photogrammetry, the science of using photography to help measure distances between objects. 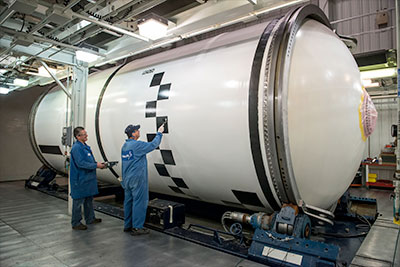 Above: Booster production is on target at prime contractor Orbital ATK's facilities, where technicians are applying photogrammetric markings on completed segments for the five-segment solid rocket booster motors for the first integrated mission of SLS and Orion. (Orbital ATK) In addition to the boosters, black-and-white photogrammetric targets will also appear on the SLS core stage, the interim cryogenic propulsion stage and the Orion stage adapter. On Orion, NASA's deep-space exploration spacecraft, photogrammetric markings will appear on the spacecraft adapter. The mobile launcher will also have photogrammetric markings. In addition, certain elements of the integrated stack, like the launch vehicle stage adapter, have photogrammetric markings on the interior rather than the exterior. Cameras will be located on Orion, on the rocket's core stage, on the interior of the launch vehicle stage adapter, on the ground and on the mobile launcher. The cameras will be able to more easily track the vehicle's position in space by fixing on the black-and-white checkerboard targets. NASA's photogrammetry analysts will then use software to process the images from the cameras to measure distances, such as between the boosters and the core stage after those elements separate. Engineers are also interested in measuring the booster nozzles' clearance from the mobile launcher and the entire vehicle's clearance from the mobile launch tower shortly after liftoff. One area engineers are particularly interested in is how the SLS solid rocket boosters, the largest ever manufactured for flight, will separate from the core stage. "Booster separation is influenced by several factors — their length, the configuration of the separation motors and the timing of separation," explained Alex Priskos, SLS systems engineering & integration manager. "The longer separation is delayed, the greater the clearance will be. However, waiting longer adversely impacts performance. Our job is to balance these factors." Engineers designed SLS using state-of-the-art 3D software models and analysis, explained Beth St. Peter, SLS imagery integration lead. "As accurate as those models are, photogrammetry will provide real-life 'truth data' on separation events and other key points. And for the first flight of SLS, gathering this real-world data on how the vehicle performs compared to the models is crucial." Although NASA has used photogrammetry since the days of the Saturn moon rockets and the space shuttle, use of the technology has come a long way, St. Peter said, primarily due to advances in being able to place digital imagery systems on launch vehicles. SLS and Orion will incorporate different types of checkerboard patterns, or photogrammetric targets, which will be used for different types of measurements, noted David Melendrez, Orion's lead for imagery integration at Johnson Space Center. "The big squares will be used to measure general vehicle motion and ground clearances. Smaller checkerboards and elongated markings will be used to measure more complicated three-dimensional motions of the boosters relative to the core stage during their separation, about two minutes into the spaceflight." 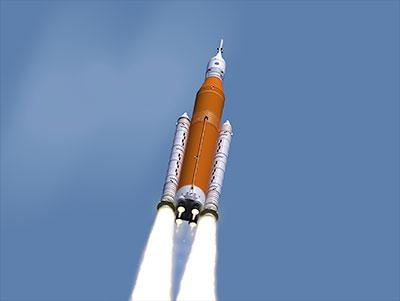 Above: Black-and-white checkerboard targets on the exterior of the Space Launch System heavy-lift rocket will enable photogrammetrists to measure critical distances during spaceflight, including booster separation from the core stage. (NASA) On some parts of the rocket, smaller circular markings will help the cameras and photogrammetric software measure separation events, like Orion's separation from the interim cryogenic propulsion stage. "Some of these smaller markings will also have retro-reflective centers to help improve our ability to see them under the dark conditions we're likely to encounter on-orbit," Melendrez said. In the final design, the photogrammetric checkerboards will replace the orange and gray stripes that had been previously considered. "Designing and building these deep space exploration systems is an evolutionary process," Priskos said. "In the beginning, you define a mission and a basic architecture to take you where you want to go. The details might be a little fuzzy at first, but gradually, like a camera zooming in closer and closer, those details are revealed. This is where we are with SLS and Orion." On launch day — and during the duration of the first mission — it won't just be the engineers on the ground who see the imagery from the cameras located at various spots on the vehicle and ground. "Some cameras will record imagery onboard SLS and Orion and transmit later. But there will also be some live downlinked imagery from these cameras on launch day," Melendrez said. "People watching at home will be able to see some of this imagery live on NASA TV." With the application of black-and-white photogrammetric targets on the solid rocket boosters, NASA's new capability for exploring deep space is becoming clearer — and closer — all the time. |
Robert Pearlman Editor Posts: 51606 From: Houston, TX Registered: Nov 1999
|
posted 08-22-2017 08:52 AM
Lockheed Martin release Lockheed Martin Powers-up Next Orion Spacecraft for First TimeEngineers at Lockheed Martin and NASA breathed life into the next Orion crew module when they powered up the spacecraft for the first time at the Kennedy Space Center, Florida. Designed for human spaceflight, this Orion will be the first to fly more than 40,000 miles beyond the Moon during its nearly three-week Exploration Mission-1 (EM-1), a feat that hasn't been possible before. "Orion was designed from the beginning to take humanity farther into space than we've ever gone, and to do this, its systems have to be very robust and reliable," said Mike Hawes, vice president and Orion program manager at Lockheed Martin. "Over the last year, we've built great momentum in assembling the crew module for EM-1. Everyone on the team understands how crucial this test campaign is, and more importantly, what this spacecraft and mission means to our country and future human space flight." The initial power-on event was the first time the vehicle management computers and the power and data units were installed on the crew module, loaded with flight software and tested. Evaluating these core systems, thought of as the "brain and heart" of the Orion capsule, is the first step in testing all of the crew module subsystems. Although astronauts will not fly in this capsule on this flight, a large majority of the subsystems and avionics are the same design that astronauts will rely on during following missions with Orion into the solar system. Launching on NASA's Space Launch System — the most powerful rocket in the world — the EM-1 flight is critical to confirming the Orion spacecraft and all of its interdependent systems operate as designed in the unforgiving environment of deep space. With the successful initial power on behind them, engineers and technicians will now continue integrating the 55 components that make up the spacecraft avionics suite, connecting them with nearly 400 harnesses. Over the course of the next two to three months, as each system is installed, they will perform thorough functional tests to ensure Orion is ready to move to the all-important environmental testing phase. |
Robert Pearlman Editor Posts: 51606 From: Houston, TX Registered: Nov 1999
|
posted 09-06-2017 07:21 PM
NASA photo release NASA Completes Welding of Liquid Oxygen Tank for First SLS FlightNASA is another step closer to completing all main structures for the agency’s first launch of the Space Launch System deep space rocket. The liquid oxygen flight tank was recently built in the Vertical Assembly Center robotic welder at NASA's Michoud Assembly Facility in New Orleans. After the liquid oxygen tank was inspected, it was moved to another area for plug welding to fill the holes left by the friction stir welding process. Five major parts — the engine section, liquid hydrogen tank, intertank, liquid oxygen tank and forward skirt — will be connected together to form the 212-foot-tall core stage, the backbone of the SLS rocket. Boeing, the prime contractor for the core stage, is welding the liquid hydrogen tank structure — the final major core stage structure to be built for the first integrated flight of SLS and Orion. The liquid hydrogen and liquid oxygen tanks will hold 733,000 gallons of propellant to power the stage's four RS-25 engines that together produce more than 2 million pounds of thrust. 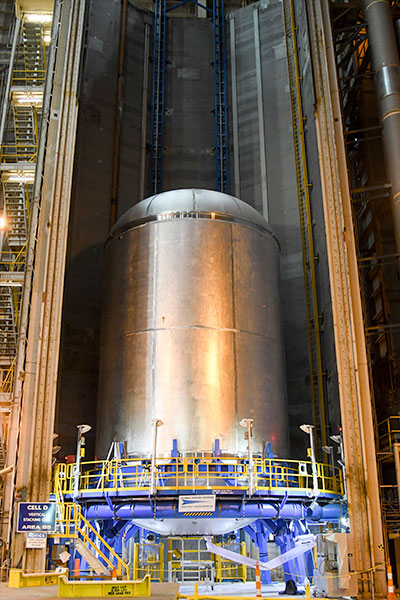 |
Robert Pearlman Editor Posts: 51606 From: Houston, TX Registered: Nov 1999
|
posted 09-29-2017 01:27 PM
NASA release NASA Completes Core Stage Hardware for First Space Launch System FlightAfter completing major welding on the liquid hydrogen tank for NASA's Space Launch System's (SLS) first flight, all five parts of the rocket's core stage are built and ready for additional outfitting and testing. NASA also finished manufacturing all four core stage test articles, and testing is underway on the engine section structural test article at NASA's Marshall Space Flight Center in Huntsville, Alabama. "The big items are done, and the team is focused on the intricate details of outfitting the flight hardware to perform specific tasks for the most powerful rocket in the world," said Chad Bryant, the SLS core stage manufacturing lead at Marshall. "When assembled, the core stage will stand taller than a 20-story building and include hundreds of cables for everything from data collection to propulsion systems." Outfitting the Core Stage 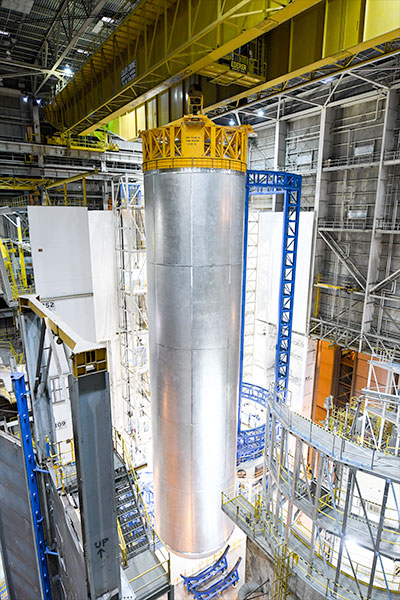 Above: NASA completed major welding for the liquid hydrogen tank for the first Space Launch System mission at the agency's Michoud Assembly Facility in New Orleans. The tank was the final piece of flight hardware completed for the deep-space rocket's first mission. All five of the structures that will be joined to form the 212-foot-tall core stage, the backbone of the SLS rocket, are built. The liquid hydrogen tank measures more than 130 feet tall, comprises almost two-thirds of the core stage and holds 537,000 gallons of liquid hydrogen cooled to minus 423 degrees Fahrenheit. (NASA/MSFC/MAF/Jude Guidry) Three core stages parts that require the most work inside are the engine section, where the four RS-25 engines will be housed, and the intertank and forward skirt that hold most of the avionics, or the brains of the rocket, that tell it how and where to fly. "Think about this work like building a car," explained Bryant. "We have the main structure or frame built. Now, we are installing the guts and electronics that turn the rocket into a transportation system: propulsion systems in the engine section, computer and other electronics in the forward skirt and the intertank." Then, to keep cryogenic propellant as cold as minus 423 degrees Fahrenheit and to protect the rocket against the harsh temperature environments experienced during launch and flight, engineers apply thermal protection insulation to every large piece on the outside as well as in critical places on the inside. Testing the Tanks To build the two largest core stage structures — the liquid hydrogen and liquid oxygen tanks that hold more than 700,000 gallons of propellant — NASA welded the thickest structures ever joined using self-reacting friction stir welding. The Vertical Assembly Center, the world's largest robotic welder at NASA's Michoud Assembly Facility in New Orleans, did the job. NASA and Boeing, the core stage prime contractor, had to overcome challenges to weld aluminum at the thicknesses required for the massive rocket tanks. 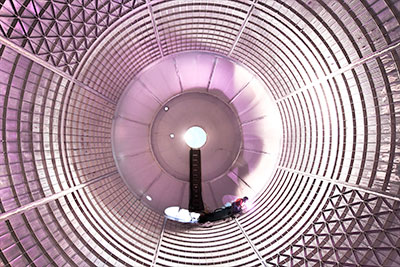 Above: The liquid oxygen tank — shown here as technicians inside the tank complete final welds to plug holes left by the robotic welder — is undergoing the first hydrostatic testing for NASA's deep-space rocket, the Space Launch System (SLS). The tank is filled with around 200,000 gallons of water that will simulate the propellant, loads, pressure and mass of the liquid oxygen. This test ensures that welds will hold to the right strength when exposed to forces similar to those experienced during launch and flight. (NASA/MSFC/MAF/Jude Guidry) The liquid oxygen tank is undergoing hydrostatic testing, which tests the weld strength by filling the tank with 200,000 gallons of water and subjecting the tank to similar pressures and forces that it will experience during flight. "This is the first time we are doing this test for an SLS tank, and it's a major milestone," said Ben Birkenstock, SLS stages manufacturing engineer at Marshall. "We've covered the tank with sensors, and we'll collect data to show the tank welds hold up when it is loaded with water that simulates propellant." The liquid hydrogen tank is being plug welded to fill in holes left during the robotic welding process, and then it will undergo a different type of proof testing using nitrogen gas and load cells to simulate pressures and loads seen during flight. The liquid hydrogen structural qualification test article already completed this proof test. SLS Pathfinder: Paving the Way for Core Stage Operations 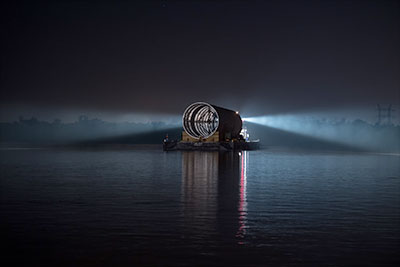 Above: The Space Launch System (SLS) core stage pathfinder, which is similar in similar in size, shape and weight to the 212-foot-tall core stage, arrived at NASA's Michoud Assembly Facility early in the morning on September 27, 2017. To reduce the risk of first-time operations with one-of-a-kind spaceflight hardware for SLS, the agency built a core stage pathfinder. Like SLS, the core stage pathfinder will be doing something that's never been done — testing new shipping and handling equipment and procedures from the manufacturing site to the test site to the launch site. (NASA/MSFC/MAF/Steven Seipel) The SLS core stage pathfinder arrived at Michoud on September 27, and now, the team will use it to hone upcoming SLS operations. The SLS pathfinder mockup and other ground support equipment are helping NASA prepare for upcoming operations with the entire core stage. Critical operations include assembling and moving the core stage at Michoud, transporting the core stage on NASA's barge Pegasus to the agency's Stennis Space Center in Bay St. Louis, Mississippi, and lifting it into the giant B-2 test stand where it will be hot-fired in a crucial pre-launch test called "the green run." After a successful test, Pegasus will take the entire stage to NASA's Kennedy Space Center in Florida, where it will be integrated with the rest of the SLS hardware and Orion. The core stage pathfinder, built and assembled at G&G Steel in Cordova, Alabama, is the same size, shape, and weight as the core stage, and it will help NASA develop and practice all these crucial logistics and operations. Dynetics Corporation of Huntsville will be completing final outfitting of pathfinder and will turn it over to NASA in early October. "NASA did not want to do complex operations for the first time with a one-of-a-kind piece of flight hardware," said Tim Flores, manager for stages ground support equipment. "The SLS core stage pathfinder will allow us to practice all these critical maneuvers with a dimensional replica of the core stage that is the same size, shape and weight as the valuable flight hardware." |
Robert Pearlman Editor Posts: 51606 From: Houston, TX Registered: Nov 1999
|
posted 10-11-2017 04:54 PM
Aerojet Rocketdyne release RS-25 Engines Ready for Maiden Flight of NASA's Space Launch SystemAerojet Rocketdyne, a subsidiary of Aerojet Rocketdyne Holdings, Inc., announces the four RS-25 engines slated to fly on Exploration Mission-1 (EM-1), the maiden flight of NASA's Space Launch System (SLS), are ready for integration with the rocket's core stage. 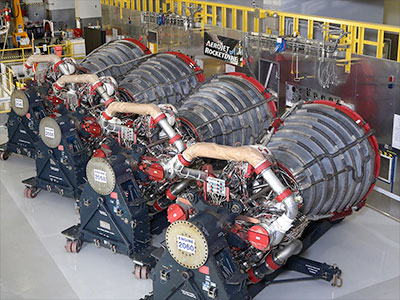 Above: Aerojet Rocketdyne displays the four RS-25 engines slated to fly on EM-1, the maiden flight of NASA's SLS rocket, at its facility located at NASA's Stennis Space Center. EM-1 is a three-week mission in which the SLS rocket will launch the Orion spacecraft into a distant retrograde orbit around the moon farther than a human-rated vehicle has traveled before, and also will deliver 13 small satellites to deep space. "The Space Launch System epitomizes our nation's legacy of ingenuity and our spirit of exploration," said Aerojet Rocketdyne CEO & President Eileen Drake. "When it launches, SLS will eclipse the performance of any rocket flying today or currently under development." All four of the RS-25 engines that will fly during EM-1 also flew during the Space Shuttle Program; however, they have been outfitted with new controllers and adapted for SLS. Each engine provides half a million pounds of thrust, totaling more than 2 million pounds of thrust, for the first stage of the SLS rocket. An infographic about the first four engines and their flight history can be found here. "These four EM-1 engines have a rich and storied history," said Dan Adamski, RS-25 program director at Aerojet Rocketdyne. "Together, they've powered 21 shuttle flights with the most experienced engine, E2045, having flown on 12 separate flights." Aerojet Rocketdyne will store the four engines for EM-1 at its facility located at NASA's Stennis Space Center until they are ready for integration with the core stage, which is currently in development at NASA's Michoud Assembly Facility in New Orleans. In addition to the core stage propulsion for the debut SLS flight, Aerojet Rocketdyne is also providing an RL10B-2 engine for the rocket's upper stage, which is called the Interim Cryogenic Propulsion Stage (ICPS). The RL10B-2 produces 24,750 pounds of thrust and is the main propulsion once the rocket has reached outer space; it gives the Orion spacecraft the final boost to complete its mission around the Moon. Earlier this year, NASA delivered the completed ICPS to Cape Canaveral Air Force Station, Florida, in preparation for integration with the rocket. "The propulsion for SLS is just one example of how all the pieces for Exploration Mission-1 are starting to come together. It is remarkable that our nation will soon debut this new capability that will enable humans to explore deep space," added Drake. |
Robert Pearlman Editor Posts: 51606 From: Houston, TX Registered: Nov 1999
|
posted 11-08-2017 06:06 PM
NASA release NASA Completes Review of First SLS, Orion Deep Space Exploration MissionNASA is providing an update on the first integrated launch of the Space Launch System (SLS) rocket and Orion spacecraft after completing a comprehensive review of the launch schedule. This uncrewed mission, known as Exploration Mission-1 (EM-1) is a critical flight test for the agency's human deep space exploration goals. EM-1 lays the foundation for the first crewed flight of SLS and Orion, as well as a regular cadence of missions thereafter near the Moon and beyond. The review follows an earlier assessment where NASA evaluated the cost, risk and technical factors of adding crew to the mission, but ultimately affirmed the original plan to fly EM-1 uncrewed. NASA initiated this review as a result of the crew study and challenges related to building the core stage of the world's most powerful rocket for the first time, issues with manufacturing and supplying Orion's first European service module, and tornado damage at the agency's Michoud Assembly Facility in New Orleans. "While the review of the possible manufacturing and production schedule risks indicate a launch date of June 2020, the agency is managing to December 2019," said acting NASA Administrator Robert Lightfoot. "Since several of the key risks identified have not been actually realized, we are able to put in place mitigation strategies for those risks to protect the December 2019 date." The majority of work on NASA's new deep space exploration systems is on track. The agency is using lessons learned from first time builds to drive efficiencies into overall production and operations planning. To address schedule risks identified in the review, NASA established new production performance milestones for the SLS core stage to increase confidence for future hardware builds. NASA and its contractors are supporting ESA's (European Space Agency) efforts to optimize build plans for schedule flexibility if sub-contractor deliveries for the service module are late. NASA's ability to meet its agency baseline commitments to EM-1 cost, which includes SLS and ground systems, currently remains within original targets. The costs for EM-1 up to a possible June 2020 launch date remain within the 15 percent limit for SLS and are slightly above for ground systems. NASA's cost commitment for Orion is through Exploration Mission-2. With NASA's multi-mission approach to deep space exploration, the agency has hardware in production for the first and second missions, and is gearing up for the third flight. When teams complete hardware for one flight, they're moving on to the next. As part of the review, NASA now plans to accelerate a test of Orion's launch abort system ahead of EM-1, and is targeting April 2019. Known as Ascent-Abort 2, the test will validate the launch abort system's ability to get crew to safety if needed during ascent. Moving up the test date ahead of EM-1 will reduce risk for the first flight with crew, which remains on track for 2023. Technology Advancements On both the rocket and spacecraft, NASA is using advanced manufacturing techniques that have helped to position the nation and U.S. companies as world leaders in this area. For example, NASA is using additive manufacturing (3-D printing) on more than 100 parts of Orion. While building the two largest core stage structures of the rocket, NASA welded the thickest structures ever joined using self-reacting friction stir welding. SLS has completed welding on all the major structures for the mission and is on track to assemble them to form the largest rocket stage ever built and complete the EM-1 "green run," an engine test that will fire up the core stage with all four RS-25 engines at the same time. NASA is reusing avionics boxes from the Orion EM-1 crew module for the next flight. Avionics and electrical systems provide the "nervous system" of launch vehicles and spacecraft, linking diverse systems into a functioning whole. For ground systems, infrastructure at NASA's Kennedy Space Center in Florida is intended to support the exploration systems including launch, flight and recovery operations. The center will be able to accommodate the evolving needs of SLS, Orion, and the rockets and spacecraft of commercial partners for more flexible, affordable, and responsive national launch capabilities. EM-1 will demonstrate safe operations of the integrated SLS rocket and Orion spacecraft, and the agency currently is studying a deep space gateway concept with U.S. industry and space station partners for potential future missions near the Moon. "Hardware progress continues every day for the early flights of SLS and Orion. EM-1 will mark a significant achievement for NASA, and our nation's future of human deep space exploration," said William Gerstenmaier, associate administrator for NASA's Human Exploration and Operations Mission Directorate in Washington. "Our investments in SLS and Orion will take us to the Moon and beyond, advancing American leadership in space." |
Robert Pearlman Editor Posts: 51606 From: Houston, TX Registered: Nov 1999
|
posted 02-16-2018 07:19 PM
European Space Agency (ESA) release Orion stage adaptor completeThe stage adaptor that will connect the Space Launch System to Orion for its first mission is nearing completion. At the top, the Orion stage adaptor connects to Orion’s spacecraft adaptor, which sits directly below the European Service Module. At the bottom, the Orion stage adopter connects to the interim cryogenic propulsion stage that will give Orion its boost towards the Moon. But the Orion stage adaptor has another trick up its sleeve: holding and launching 13 cubesats and housing an avionics unit. 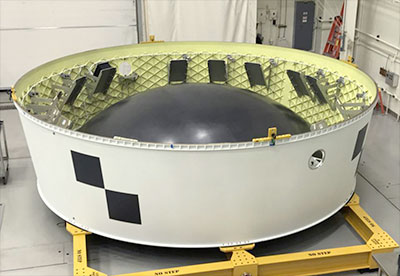 The 13 CubeSat 6U payloads are each the size of a large shoebox and weigh about 14 kg. They will hitch a ride to deep space safely stowed in the Orion stage adaptor and will include NASA research experiments and spacecraft developed by industry, international, and academic partners. The CubeSats will be deployed after Orion separates from the Space Launch System. The Orion stage adaptor diaphragm (in black in these photos) provides a barrier to launch vehicle gases — such as hydrogen — from entering the Orion spacecraft, where astronauts will ride to lunar orbit on the second Exploration mission. The diaphragm is constructed of multiple layers of carbon-fibre with epoxy. The Orion stage adaptor measures about 5.5 m in diameter and 1.5 m tall. 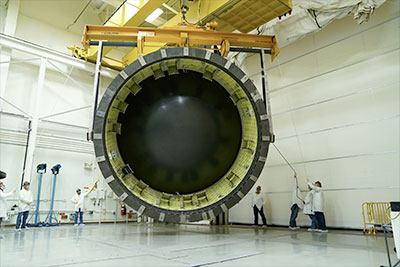 |
Robert Pearlman Editor Posts: 51606 From: Houston, TX Registered: Nov 1999
|
posted 04-24-2018 11:12 AM
NASA release Simulated Countdown Another Step Toward Exploration Mission-1"NTD you are GO to proceed with the count." With words such as these, NASA Launch Director Charlie Blackwell-Thompson will authorize the NASA Test Director, whose call sign is NTD, to proceed with launching the agency's Space Launch System (SLS) rocket and Orion spacecraft on Exploration Mission-1 (EM-1), the first integrated test of the new vehicles. SLS and Orion are part of NASA’s deep space exploration systems designed to send humans to distant destinations, such as the Moon and Mars. An important step in preparation for that first flight took place on March 29 with a demonstration of a portion of the countdown focused on fueling the new launch vehicle. 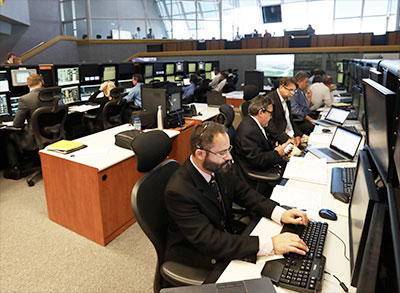 Above: Plans for call for about 91 engineers and managers to serve on the Space Launch System-Orion Firing Room launch team, less than half the number supporting a space shuttle countdown. (NASA/Cory Huston) "This demonstration is important because we are getting an early feel for our tanking operations, the timelines for this work and the kinds of issues that can arise," said Blackwell-Thompson. "We've already started writing our launch countdown procedures for SLS and having an opportunity to run through those operations is extremely beneficial. What we learn from this demonstration and other simulations to come will be rolled into our launch countdown processes and procedures." A veteran engineer who has worked at Kennedy since 1988, Blackwell-Thompson will lead the launch team for the first flight test of this next-generation launch system. As launch director, she will make the final "go/no-go" decision prior to liftoff. The NTD is the leader of the SLS test team and is responsible for directing and integrating all flight and ground support testing throughout the countdown. For EM-1, the countdown is expected to take about 45 hours and 40 minutes beginning two days prior to liftoff. During that time, the SLS core stage and upper stage will require about six hours to load 730,000 gallons of cryogenic liquid hydrogen and liquid oxygen to fuel the four core stage and single upper stage engines. The countdown is a carefully planned set of procedures leading up to ignition of a rocket's engine and liftoff. For the recent demonstration, the countdown began at the L-minus 16-hour mark when activities included preparations for propellant loading, and later skipped ahead in the count, altogether taking about five hours. While there was no SLS at Kennedy's Launch Complex 39B for the simulation, software called an "emulator" provided a virtual experience of what would be happening with the rocket. The simulated countdown took place in Firing Room 1 of Kennedy's Launch Control Center, which is where the team will be on launch day. The firing rooms are the heart of the center's command and control system. All activities involved with preparing rockets, spacecraft and payloads are controlled by NASA and contractor managers and engineers seated at computer terminals. Likewise, all activities at the launch pads can be operated from a firing room. During the recent simulation, the launch team became acquainted with new consoles, improved software and the procedures for the SLS. 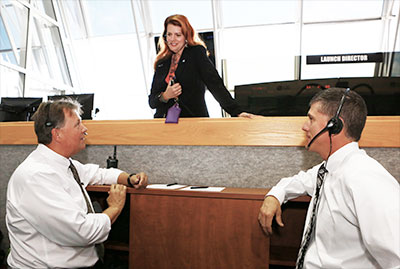 Above: NASA Launch Director Charlie Blackwell-Thompson, above, confers with Senior NASA Test Director Jeff Spaulding, left, and Chief NASA Test Director Jeremy Graeber in Firing Room 1 at the Kennedy Space Center's Launch Control Center during a countdown demonstration for Exploration Mission-1. (NASA/Cory Huston) "It was important to get the launch team in the Firing Room, practicing reporting protocols, taking a look at our displays, and seeing how our emulators and simulators perform," said Blackwell-Thompson. "What we learn here will help us determine where changes are needed as we progress. There will no doubt be adjustments, but the Firing Room is now set up, pretty much, as it will be on EM-1 launch day." Much work and many more multifaceted countdown simulations remain before the launch team will be ready for the first SLS lift-off. Blackwell-Thompson noted that in took a lot of work to get ready for the recent demonstration, and praised the launch team for their outstanding efforts. "When I think about this team, I think about their skill, the expertise, the love and the passion they bring to their work," she said. "They are outstanding, and I feel blessed to work with such amazing people. I am confident that this team will be ready for the work ahead and any challenges that come on launch day." The first in a series of increasingly complex missions, EM-1 will be an unpiloted flight test that will provide a foundation for human deep space exploration. During this flight, Orion will travel 280,000 miles from Earth, thousands of miles beyond the Moon over the course of about a three-week mission. The second flight of Orion, Exploration Mission-2, will carry crew to test the spacecraft's crucial systems and prepare for future missions to the Moon, and eventually to Mars. |
Robert Pearlman Editor Posts: 51606 From: Houston, TX Registered: Nov 1999
|
posted 07-31-2018 06:27 PM
NASA release First SLS Core Stage Flight Hardware Complete, Ready for JoiningThe first major piece of core stage hardware for NASA's Space Launch System rocket has been assembled and is ready to be joined with other hardware for Exploration Mission-1, the first integrated flight of SLS and the Orion spacecraft. SLS will enable a new era of exploration beyond low-Earth orbit, launching crew and cargo on deep space exploration missions to the Moon, Mars and beyond. 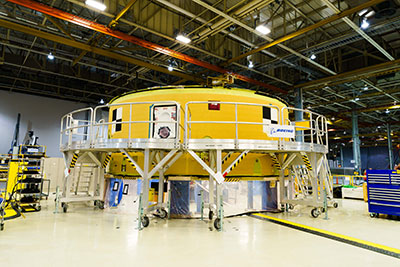 Above: The first major piece of core stage hardware for NASA's Space Launch System rocket has been assembled and is ready to be joined with other hardware for Exploration Mission-1. The forward skirt will connect the upper part of the rocket to the core stage and house many of the flight computers, or avionics. The backbone of the world's most powerful rocket, the 212-foot-tall core stage, will contain the SLS rocket's four RS-25 rocket engines, propellant tanks, flight computers and much more. Though the smallest part of the core stage, the forward skirt will serve two critical roles. It will connect the upper part of the rocket to the core stage and house many of the flight computers, or avionics. "Completion of the core stage forward skirt is a major step in NASA's progress to the launch pad," said Deborah Bagdigian, lead manager for the forward skirt at the agency's Marshall Space Flight Center in Huntsville, Alabama. "We're putting into practice the steps and processes needed to assemble the largest rocket stage ever built. With the forward skirt, we are improving and refining how we'll conduct final assembly of the rest of the rocket." On July 24, forward skirt assembly was wrapped up with the installation of all its parts. As part of forward skirt testing, the flight computers came to life for the first time as NASA engineers tested critical avionic systems that will control the rocket's flight. The construction, assembly and avionics testing occurred at NASA's Michoud Assembly Facility in New Orleans. Located throughout the core stage, the avionics are the rocket's "brains," controlling navigation and communication during launch and flight. It is critical that each of the avionics units is installed correctly, work as expected and communicate with each other and other components, including the Orion spacecraft and ground support systems. "It was amazing to see the computers come to life for the first time" said Lisa Espy, lead test engineer for SLS core stage avionics. "These are the computers that will control the rocket as it soars off the pad for Exploration Mission-1." The forward skirt test series was the first of many that will verify the rocket's avionics will work as expected during launch. The tests show the forward skirt was built correctly, and that all components and wiring on the inside have been put together and connected properly and are sending data over the lines as expected. The avionic computers ran "built-in tests" that Espy compares to the internal diagnostic tests performed by an automobile when first started. All of the health and data status reports came back as expected. The tests were a success and did not return any error codes. Such error codes would be similar to a check engine light on a car. The successful tests give the team the confidence needed to move forward with avionics installations in the core stage intertank and engine section. With more hardware and more interfaces, the installation in the intertank will be more complex, and the complexity will ramp up even more as the team moves to the engine section, introducing hydraulics and other hardware needed for the rocket's engines. "Each piece of hardware and each test builds to the next," Espy said. "That's why we're excited about the successful forward skirt tests. They lay a solid foundation as we continue to build more and more complex components and get the rocket ready for its first launch." 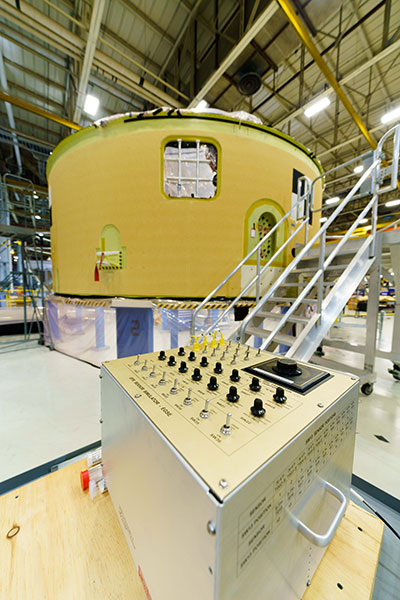 Above: Located throughout the core stage, the avionics are the rocket's "brains," controlling navigation and communication during launch and flight. The forward skirt test series was the first of many that will verify the rocket's avionics will work as expected during launch. The forward skirt is now ready to be joined with the rest of the rocket's core stage. Integration of the massive core stage will take place in two joins, the forward join — including the forward skirt, liquid oxygen tank and intertank — and the aft join — including the liquid hydrogen tank and the engine section. Engineers will perform standalone tests on each component as they are completed. Once the forward and aft joins are integrated, they will perform a final integrated function test, testing all the core stage's avionics together. The fully integrated core stage and its four RS-25 engines will then be fired up during a final test before launch. At NASA's Kennedy Space Center in Florida, the core stage will be stacked with the upper part of the rocket, including Orion, and joined to the rocket's twin solid rocket boosters, in preparation for EM-1. |
Robert Pearlman Editor Posts: 51606 From: Houston, TX Registered: Nov 1999
|
posted 08-16-2018 05:47 PM
NASA release Heat Shield Install Brings Orion Spacecraft Closer to SpaceDuring Exploration Mission-1 (EM-1), an uncrewed Orion spacecraft will launch atop NASA's Space Launch System rocket and begin a three-week voyage in space, taking it about 40,000 miles beyond the Moon and back to Earth. On its return, the spacecraft's heat shield will need to withstand temperatures of nearing 5,000 degrees Fahrenheit during its fiery re-entry through the Earth's atmosphere before it splashes down in the Pacific Ocean. 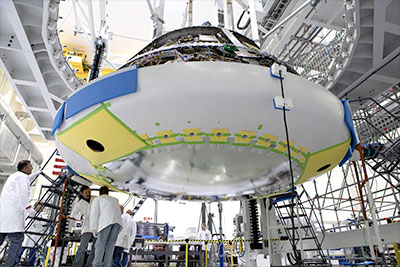 Above: Lockheed Martin engineers and technicians check fittings during installation of the heat shield to the Orion crew module July 25, 2018, inside the Neil Armstrong Operations and Checkout Building high bay at NASA's Kennedy Space Center in Florida. (NASA/Kim Shiflett) Technicians at NASA's Kennedy Space Center (KSC) in Florida recently secured the heat shield to the bottom of the crew module, using 68 bolts. Designed and manufactured by Orion prime contractor, Lockheed Martin, the heat shield is like an intricate puzzle with pieces that all have to fit together perfectly. Before the final installation, a fit check was performed to ensure all of the bolt fittings lined up. "Installation of the EM-1 crew module heat shield is a significant milestone representing the beginning of closing out the crew module assembly," said Jules Schneider, Lockheed Martin Orion senior manager for KSC Operations. "When the heat shield is installed, access to components becomes more difficult, and in some cases there is no more access. So by installing the heat shield you are declaring that a certain percentage of the spacecraft is finished." Measuring 16.5 feet in diameter, Orion's new heat shield is the largest of its kind developed for missions that will carry astronauts. The heat shield base structure has a titanium truss covered with a composite substrate, or a skin composed of layers of carbon fiber material. In a new process, several large blocks of an ablative material called Avcoat, licensed from Boston-based Textron Systems, were produced at Michoud Assembly Facility in New Orleans by Lockheed Martin. They were shipped to Kennedy, where Lockheed Martin technicians machined them into more than 180 unique blocks and bonded them to the heat shield's surface. To fill tiny gaps between the blocks, the seams were filled with a mixture that over time will become solid. Technicians applied a coat of white epoxy paint to the heat shield's surface and then applied aluminized tape after the painted surface dried. The tape provides surface resistivity, and absorbs solar heat and infrared emissions. "Witnessing assembly, test and installation of the EM-1 crew module heat shield brought an appreciation for its innovative design and assembly techniques," said Amy Marasia, the Crew Module Assembly operations lead in NASA's Orion Production Operations. 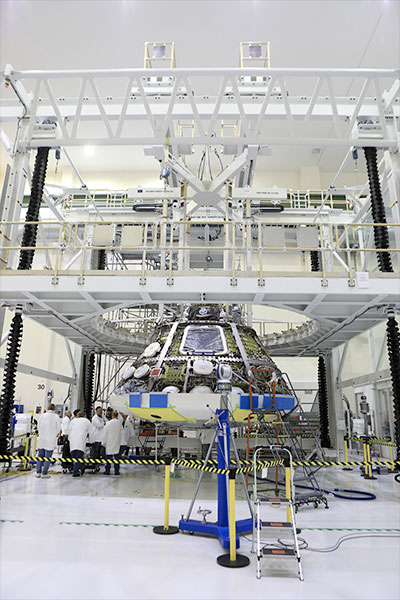 Above: Lockheed Martin engineers and technicians install the heat shield to the Orion crew module July 25, 2018, inside the Neil Armstrong Operations and Checkout Building high bay at NASA's Kennedy Space Center in Florida. (NASA/Kim Shiflett) While Avcoat isn't new to spacecraft – it was used on the heat shields of Apollo and the Orion Exploration Flight Test-1 – the technique of using blocks instead of injecting the ablative material is proving to be a real production time-saver. "A benefit of switching from the honeycomb system to the blocks is we now can make the Avcoat blocks at the same time that the Orion structure is being made, and when the module is ready we can secure the blocks, which saves time," said John Kowal, NASA Orion Thermal Protection System manager at Johnson Space Center in Houston. "Before, with EFT-1, we had to wait for the carrier portion to be done, and then apply the Avcoat directly to the crew module." During its first mission around the Moon, engineers will monitor how Orion's systems perform in the environment of deep space and its return to Earth. During re-entry the ablative material of the Avcoat blocks will burn away, essentially carrying the heat away from Orion because of the gases created during the ablative process. |
Robert Pearlman Editor Posts: 51606 From: Houston, TX Registered: Nov 1999
|
posted 11-06-2018 09:47 PM
NASA release European-Built Service Module Arrives in U.S. for First Orion Moon MissionThe powerhouse that will help NASA's Orion spacecraft venture beyond the Moon is stateside. The European-built service module that will propel, power and cool during Orion flight to the Moon on Exploration Mission-1 arrived from Germany at the agency's Kennedy Space Center in Florida on Tuesday to begin final outfitting, integration and testing with the crew module and other Orion elements. 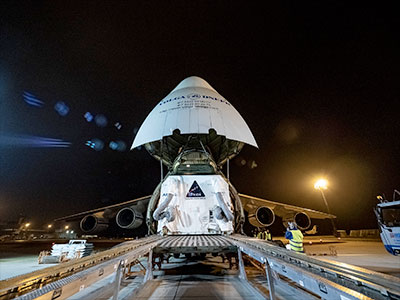 Above: The European Service Module for NASA's Orion spacecraft is loaded on an Antonov airplane in Bremen, Germany, on Nov. 5, 2018, for transport to NASA's Kennedy Space Center in Florida. For the first time, NASA will use a European-built system as a critical element to power an American spacecraft, extending the international cooperation of the International Space Station into deep space. (NASA/Rad Sinyak) The service module is integral to human missions to the Moon and Mars. After Orion launches on top of the agency's Space Launch System rocket, the service module will be responsible for in-space maneuvering throughout the mission, including course corrections. The service module will also provide the powerful burns to insert Orion into lunar orbit and again to get out of lunar orbit and return to Earth. It is provided by ESA (European Space Agency) and built by ESA's prime contractor Airbus of Bremen, Germany. NASA's prime contractor for Orion, Lockheed Martin, built the crew module and other elements of the spacecraft. "We have a strong foundation of cooperation with ESA through the International Space Station partnership, and the arrival of the service module signifies that our international collaboration extends to our deep space human exploration efforts as well," said Bill Gerstenmaier, NASA's associate administrator for Human Exploration and Operations. The European-built service module brings together new technology and lightweight materials while taking advantage of spaceflight-proven hardware. It is comprised of more than 20,000 components, including four solar array wings that provide enough electricity to power two three-bedroom homes, as well as an orbital maneuvering system engine, a recently refurbished engine previously used for in-orbit control by the space shuttle. Beginning with Exploration Mission-2, the module also will provide air and water for astronauts flying inside Orion, which will carry people to destinations farther than anyone has travelled before and return them safely to Earth. "Our teams have worked together incredibly hard to develop a service module that will make missions to the Moon and beyond a reality," said Mark Kirasich, NASA's Orion program manager. "It is quite an accomplishment of ESA and Airbus to have completed the developmental work on the module and have this major delivery milestone behind us." Now that the service module is at Kennedy, it will undergo a host of tests and integration work ahead of Exploration Mission-1. Engineers will complete functional checkouts to ensure all elements are working properly before it is connected to the Orion crew module. Teams will weld together fluid lines to route gases and fuel and make electrical wiring connections. The service module and crew module will be mated, and the combined spacecraft will be sent to NASA's Glenn Research Center's Plum Brook Station in Ohio early next year where it will undergo 60 days of continuous testing in the world's largest thermal vacuum chamber to ensure Orion can withstand the harsh environment of deep space. Once that testing is complete, it will return to Kennedy for integration with the SLS rocket in preparation for launch. |
Robert Pearlman Editor Posts: 51606 From: Houston, TX Registered: Nov 1999
|
posted 01-11-2019 05:31 PM
From Northrop Grumman on Twitter: We are excited to announce that we have completed the final solid rocket motor for the first Space Launch System flight! The motor will be stored at our Promontory, Utah facility while it awaits shipment to Kennedy Space Center. 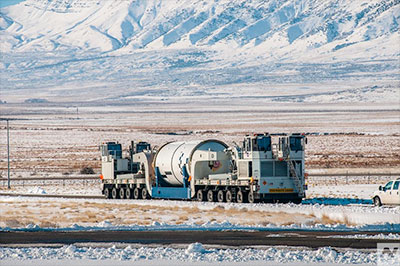 |
Robert Pearlman Editor Posts: 51606 From: Houston, TX Registered: Nov 1999
|
posted 03-22-2019 11:28 PM
NASA release SLS Engine Section Approaches Finish Line for First FlightNASA and Boeing have completed the majority of outfitting for the core stage engine section for the first flight of the agency's new Space Launch System (SLS) rocket. The engine section, located at the bottom of the 212-foot-tall core stage, is one of the most complex parts of the rocket. Technicians at NASA's Michoud Assembly Facility in New Orleans have installed more than 500 sensors, 18 miles of cables, and numerous other critical systems for mounting, controlling and delivering fuel to the rocket's four RS-25 engines. 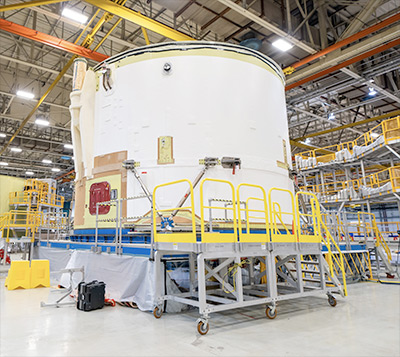 The core stage tanks hold cryogenic liquid hydrogen and liquid oxygen that are combusted by the engines to produce 2 million pounds of thrust to help send SLS to space for missions to the Moon. On the exterior of the engine section, technicians attached cork insulation for thermal protection and painted it white as well as finishing up other systems including fittings where solid rocket boosters attach. Next, NASA and Boeing, the SLS prime contractor, will add the boat-tail to the bottom of the engine section and finish up some outfitting, integration and avionics functional testing. The boat-tail is an extension that fits on the end of the engine section. The engines are inserted through openings in the boat-tail, which acts much like a fairing to cover and protect most of engines' critical systems. The engines are mounted inside the engine section, and only the RS-25 engine nozzles extend outside the boat-tail. The team is using lessons learned building and outfitting the engine section for the first integrated flight of SLS to accelerate outfitting of the engine section for the second SLS mission. The primary structure of the core stage engine section for the second SLS flight has been built and covered with primer as it prepares for its outfitting and is visible in this image, just behind the first engine section. |
Robert Pearlman Editor Posts: 51606 From: Houston, TX Registered: Nov 1999
|
posted 06-29-2019 08:17 AM
NASA photo release Artemis 1 Engines Delivered to NASA’s Michoud Assembly FacilityCrews delivered the last of four RS-25 engines for Artemis 1, the first flight of NASA’s Space Launch System (SLS) rocket and the Orion spacecraft, from NASA’s Stennis Space Center near Bay St. Louis, Mississippi, to NASA’s Michoud Assembly Facility in New Orleans Thursday, June 27, 2019. 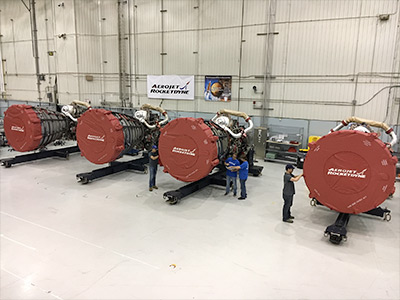 The engines, located at the bottom of the rocket’s massive core stage, are fueled by liquid hydrogen and liquid oxygen. When Artemis 1 launches to the Moon, the four RS-25 engines will fire nonstop for 8.5 minutes, providing the rocket 2 million of its 8.8 million pounds of maximum thrust at liftoff. Technicians from NASA and Aerojet Rocketdyne, the lead contractor for the engines, at Michoud will now prepare the four engines for installation to the rest of the core stage later this summer. |
Robert Pearlman Editor Posts: 51606 From: Houston, TX Registered: Nov 1999
|
posted 07-20-2019 03:17 PM
Lockheed Martin release Lockheed Martin Completes NASA's Orion Spacecraft Capsule for Artemis 1 Mission to the MoonThe goal of humans again walking on the Moon is one giant leap closer. Lockheed Martin has completed building the capsule for NASA's Orion spacecraft. The crew module capsule for the uncrewed Artemis 1 mission to the Moon has been stacked on top of the Orion service module, which was also recently finished. 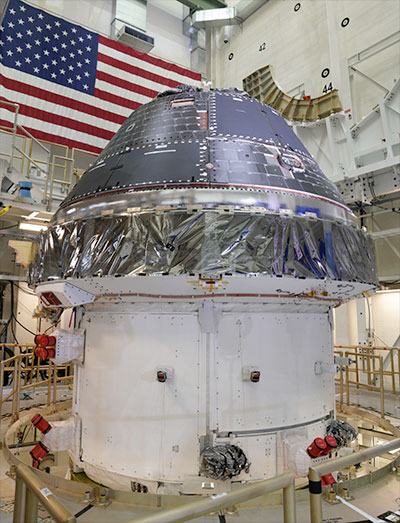 Above: On the anniversary of the Apollo Moon landing, the Lockheed Martin-built Orion capsule for the Artemis 1 mission to the Moon is declared finished. Vice President Mike Pence made the announcement today at a ceremony in front of the Orion spacecraft in the aptly-named Neil Armstrong Operations and Checkout Building at the Kennedy Space Center in Florida. The event and announcement commemorated the 50-year anniversary of the Apollo 11 Moon landing. Lockheed Martin's President, Chairman and CEO Marillyn Hewson also provided remarks at the ceremony, in addition to NASA's Administrator Jim Bridenstine, Kennedy Space Center's Director Robert Cabana and Florida's Governor Ron DeSantis. The Orion spacecraft is like none other in its design and capability. "Orion is a new class of spaceship, uniquely designed for long-duration deep space flight, that will return astronauts to the Moon and eventually take the first humans to Mars, and bring them all back safely," said Lisa Callahan, vice president and general manager of Commercial Civil Space at Lockheed Martin. "Orion will accelerate scientific discovery of our solar system and will be the cornerstone of the defining space achievement of this era." Since the crew module pressure vessel arrived in Florida, technicians and engineers from Lockheed Martin, NASA and supporting contractors have meticulously assembled the capsule into its finished state. The work included installing the capsule's avionic computers, harnesses, propulsion system and its 12 engines, 11 parachutes, its large 16-foot-diameter heat shield, forward bay cover and numerous other systems and components. "Throughout assembly, the team tested and validated the many systems a hundred different ways to ensure they will operate as designed in the harshness of deep space," said Mike Hawes, Orion program manager for Lockheed Martin. "The Artemis 1 flight will test the design and workmanship of the capsule and its service module during the three-week mission out around the Moon and back. We're excited for this mission as it paves the way for the first crewed mission in 2022, Artemis 2." The crew module and service module were stacked together earlier in the week in the Final Assembly and System Testing (FAST) cell where they are now being fully integrated, including connecting the physical retention bolts and the umbilical lines between the two modules. The FAST cell is also where the Apollo spacecraft were integrated. The combined stack will then be powered up and undergo a series of integrated systems tests. In September, the combined stack will be shipped to NASA's Plum Brook Station in Ohio, where it will go through environmental testing in a large thermal vacuum chamber as well as testing for electromagnetic interference and compatibility. Once Orion returns to Kennedy at the end of the year, the spacecraft will go through final preparations before Lockheed Martin delivers it to ground systems for launch processing in early 2020. |
Robert Pearlman Editor Posts: 51606 From: Houston, TX Registered: Nov 1999
|
posted 08-08-2019 11:27 AM
NASA photo release This image, taken Aug. 8, 2019, shows the core stage for NASA's Space Launch System (SLS) rocket at the agency's Michoud Assembly Facility in New Orleans.The core stage is 80% complete and, over the summer, engineers will add the last core stage structure – the engine section – and the four RS-25 engines. This complex stage controls the rocket's journey for the first eight minutes of flight and produces two million pounds of thrust to send SLS and NASA's Orion spacecraft on their first lunar mission, Artemis 1. Photo credit: NASA/Eric Bordelon |
Robert Pearlman Editor Posts: 51606 From: Houston, TX Registered: Nov 1999
|
posted 09-20-2019 12:34 PM
NASA release NASA Joins Last of Five Sections for Space Launch System Rocket StageNASA finished assembling and joining the main structural components for the largest rocket stage the agency has built since the Saturn V that sent Apollo astronauts to the Moon. Engineers at the agency's Michoud Assembly Facility in New Orleans connected the last of the five sections of the Space Launch System (SLS) rocket core stage on Sept. 19. The stage will produce 2 million pounds of thrust to send Artemis I, the first flight of SLS and NASA's Orion spacecraft to the Moon. 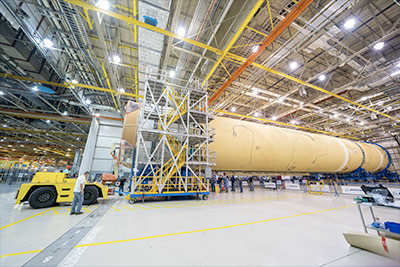 Above: NASA finished assembling the main structural components for the Space Launch System (SLS) rocket core stage on Sept. 19. Engineers at NASA’s Michoud Assembly Facility in New Orleans fully integrated the last piece of the 212-foot-tall core stage by adding the engine section to the rest of the previously assembled structure. Boeing technicians bolted the engine section to the stage’s liquid hydrogen propellant tank. (NASA/Steven Seipel) "NASA has achieved a historic first milestone by completing the final join of the core stage structure for NASA's Space Launch System, the world's most powerful rocket," said Julie Bassler, the NASA SLS stages manager. "Now, to complete the stage, NASA will add the four RS-25 engines and complete the final integrated avionics and propulsion functional tests. This is an exciting time as we finish the first-time production of the complex core stage that will provide the power to send the Artemis I mission to the Moon." The last piece added to the stage was the engine section located at the bottom of the 212-foot-tall core stage. To complete the structure, technicians bolted the engine section to the stage's liquid hydrogen propellant tank, which was recently attached to the other core stage structures. The engine section is one of the most complicated pieces of hardware for the SLS rocket and is the attachment point for the four RS-25 rockets and the two solid rocket boosters that produce a combined 8.8 millions pounds of thrust. The engine section also includes vital systems for mounting, controlling and delivering fuel from the stage's two liquid propellant tanks to the rocket's engines. This fall, NASA will work with core stage lead contractor, Boeing, and the RS-25 engine lead contractor, Aerojet Rocketdyne, to attach the four RS-25 engines and connect them to the main propulsion systems inside the engine section. "Boeing expects to complete final assembly of the Artemis I core stage in December," said Jennifer Boland-Masterson, Boeing operations direct at MAF. "After we deliver the stage, NASA will transport it on the agency's Pegasus barge from Michoud to NASA's Stennis Space Center near Bay St. Louis, Mississippi, for Green Run testing. Our team here at Michoud will continue work with NASA to build, outfit and assemble the core stage for Artemis II, the first mission that will send astronauts to orbit the Moon. Lessons learned and innovations developed in building the first core stage are making the second one progress much faster." During Green Run testing, engineers will install the core stage into the B-2 Test Stand at Stennis for a series of tests that will build like a crescendo over several months. This will be the first fully fueled test of this brand new rocket stage. Many aspects will be carried out for the first time, such as fueling and pressurizing the stage, and the test series culminates with firing up all four engines to demonstrate that the engines, tanks, fuel lines, valves, pressurization system, and software can all perform together as they will on launch day. 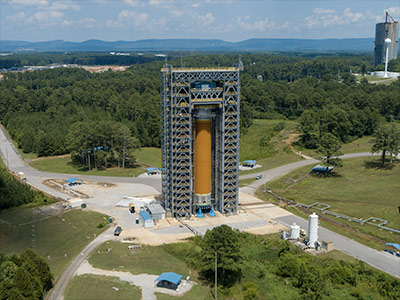 Above: The core stage test team recently completed structural testing confirming the stage’s liquid hydrogen tank structural design is good for conditions that will be experienced in the rocket’s initial configuration, called Block 1, during the Artemis I launch. (NASA/Tyler Martin) The SLS team also achieved another recent milestone by completing structural testing for the stage's liquid hydrogen tank. The testing confirmed that the structural design for the tank on the rocket's initial configuration, called Block 1, can withstand extreme conditions during launch and flight. Teams at NASA's Marshall Space Flight Center in Huntsville, Alabama, put a test version of the tank through the paces during 37 separate test cases that exceed what engineers expect the SLS rocket to experience. The final test used 80,000 gallons of liquid nitrogen to simulate the cryogenic conditions, or extreme cold, that the liquid hydrogen tank will experience in flight. Testing will continue later this year to show the tank's structural design is adequate for future designs of the vehicle as it evolves to a Block IB configuration and missions with even greater forces. In addition to providing propellant and power to get the SLS rocket and Orion spacecraft to space, the core stage houses the flight computers and avionics components that control the first 8 minutes of flight. The avionics system, including the flight computers, completed integrated system level qualification testing showing the components all work together to control the rocket in the Software Integration and Test Facility (SITF) at Marshall. The next step is to test the flight software with all the ground system software, Orion and launch control in the Systems Integration Laboratory at Marshall. "NASA and our contractor teams are making tremendous progress on every aspect of manufacturing, assembling and testing the complex systems needed to land American astronauts on the lunar surface by 2024," Bassler said. "I am confident this hard work will result in a rocket that can provide the backbone for deep space transportation to the Moon and ultimately to Mars." |
Robert Pearlman Editor Posts: 51606 From: Houston, TX Registered: Nov 1999
|
posted 10-22-2019 03:47 PM
NASA photo release (credit: NASA/Jude Guidry) NASA Attaches First of 4 RS-25 Engines to Artemis I Rocket StageEngineers and technicians at NASA’s Michoud Assembly Facility in New Orleans have structurally mated the first of four RS-25 engines to the core stage for NASA’s Space Launch System (SLS) rocket that will help power the first Artemis mission to the Moon. 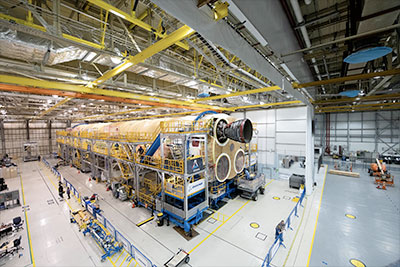 Integration of the RS-25 engines to the recently completed core stage structure is a collaborative, multistep process for NASA and its partners Boeing, the core stage lead contractor, and Aerojet Rocketdyne, the RS-25 engines lead contractor. To complete the installation, the technicians will now integrate the propulsion and electrical systems. The installation process will be repeated for each of the four RS-25 engines. The four RS-25 engines used for Artemis I were delivered to Michoud from Aerojet Rocketdyne’s facility at NASA’s Stennis Space Center near Bay St. Louis, Mississippi, in June. The engines, located at the bottom of the core stage in a square pattern, are fueled by liquid hydrogen and liquid oxygen. During launch and flight, the four engines will fire nonstop for 8.5 minutes, emitting hot gases from each nozzle 13 times faster than the speed of sound. The completed core stage with all four engines attached will be the largest rocket stage NASA has built since the Saturn V stages for the Apollo Program. |
Robert Pearlman Editor Posts: 51606 From: Houston, TX Registered: Nov 1999
|
posted 11-01-2019 12:08 PM
NASA photo release (credit: NASA/Eric Bordelon) Second RS-25 Engine Attached to NASA Moon RocketThe second RS-25 engine has been attached to the core stage for NASA's Space Launch System (SLS) rocket for the agency's Artemis missions. Engineers and technicians at NASA's Michoud Assembly Facility in New Orleans structurally mated the second of four engines to the stage on Oct. 30 and are currently integrating the propulsion and electrical systems within the structure to complete the installation. Integration of the RS-25 engines to the recently completed core stage structure is a collaborative, multistep process for NASA and its partners Boeing, the core stage lead contractor, and Aerojet Rocketdyne, the RS-25 engines lead contractor. The four RS-25 engines for Artemis I are modified heritage flight hardware from the Space Shuttle Program, ensuring high performance and reliability to power NASA's next generation lunar missions. Each engine also has a special identification number, and NASA keeps a history of which engines are used on each mission. The second engine, Engine 2045, has flown on several shuttle missions, including the mission that returned NASA astronaut John Glenn to space in 1998 as well as the first and only shuttle launch to occur on Independence Day in 2006. |
Robert Pearlman Editor Posts: 51606 From: Houston, TX Registered: Nov 1999
|
posted 11-08-2019 01:38 PM
NASA photo release (photo credit: NASA/Eric Bordelon) All Four Engines Are Attached to the SLS Core Stage for Artemis I MissionAll four RS-25 engines were structurally mated to the core stage for NASA's Space Launch System (SLS) rocket for Artemis I, the first mission of SLS and NASA's Orion spacecraft. To complete assembly of the rocket stage, engineers and technicians are now integrating the propulsion and electrical systems within the structure. The completed core stage with all four RS-25 engines attached is the largest rocket stage NASA has built since the Saturn V stages for the Apollo Program that first sent Americans to the Moon. The stage, which includes two huge propellant tanks, provides more than 2 million pounds of thrust to send Artemis I to the Moon. Engineers and technicians at NASA's Michoud Assembly Facility in New Orleans attached the fourth RS-25 engine to the rocket stage Nov. 6 just one day after structurally mating the third engine. The first two RS-25 engines were structurally mated to the stage in October. After assembly is complete, crews will conduct an integrated functional test of flight computers, avionics and electrical systems that run throughout the 212-foot-tall core stage in preparation for its completion later this year. This testing is the first time all the flight avionics systems will be tested together to ensure the systems communicate with each other and will perform properly to control the rocket's flight. Integration of the RS-25 engines to the massive core stage is a collaborative, multistep process for NASA and its partners Boeing, the core stage lead contractor, and Aerojet Rocketdyne, the RS-25 engines lead contractor. |
Robert Pearlman Editor Posts: 51606 From: Houston, TX Registered: Nov 1999
|
posted 01-02-2020 05:44 PM
NASA photo release NASA Prepares Artemis I SLS Rocket Stage for Move to Pegasus BargeTeams at NASA's Michoud Assembly Facility in New Orleans moved the core stage, complete with all four RS-25 engines, for NASA's Space Launch System (SLS) rocket to Building 110 for final shipping preparations on Jan. 1, 2020. 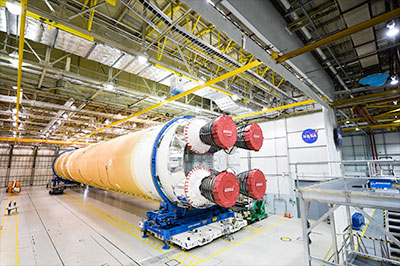 The SLS core stage includes state-of-the-art avionics, propulsion systems and two colossal propellant tanks that collectively hold 733,000 gallons of liquid oxygen and liquid hydrogen to power its four RS-25 engines. The completed stage, which will provide more than 2 million pounds of thrust to help power the first Artemis mission to the Moon, will be shipped via the agency's Pegasus barge from Michoud to NASA's Stennis Space Center near Bay St. Louis, Mississippi, later this month. Once at Stennis, the Artemis rocket stage will be loaded into the B-2 Test Stand for the core stage Green Run test series. The comprehensive test campaign will progressively bring the entire core stage, including its avionics and engines, to life for the first time to verify the stage is fit for flight ahead of the launch of Artemis I. 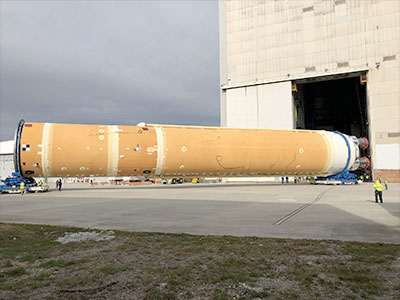 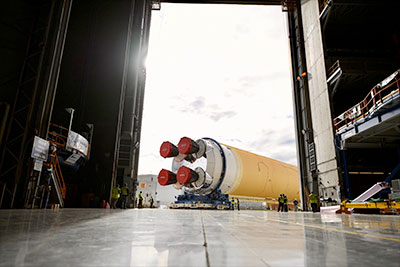
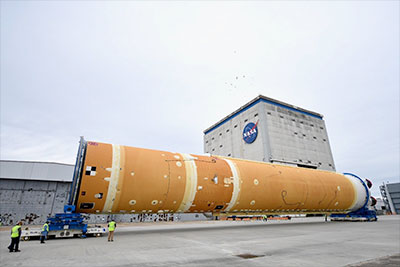 |
Robert Pearlman Editor Posts: 51606 From: Houston, TX Registered: Nov 1999
|
posted 01-08-2020 04:20 PM
NASA release First NASA Artemis Rocket Core Stage Loaded on Pegasus BargeThe first Space Launch System (SLS) rocket core stage for NASA's Artemis program completed manufacturing work at NASA's Michoud Assembly Facility in New Orleans and was loaded onto the agency's Pegasus barge on Jan. 8 for delivery to NASA's Stennis Space Center near Bay St. Louis, Mississippi. With NASA Deputy Administrator Jim Morhard in attendance, NASA rolled out the core stage for the SLS rocket onto Pegasus in preparation for the Green Run test series, the final test campaign ahead of the agency's first Artemis launch. 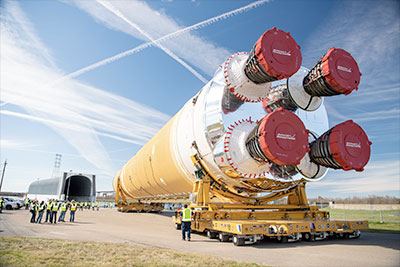 Above: The first Artemis rocket stage is guided toward NASA's Pegasus barge Jan. 8 ahead of its forthcoming journey to NASA's Stennis Space Center near Bay St. Louis, Mississippi. "NASA's Space Launch System core stage is part the Artemis program, which is a national asset," said NASA Deputy Administrator Jim Morhard. "The SLS rocket was built to deliver American astronauts and maximum payloads to the Moon and deep space destinations. Rolling out the completed core stage from NASA's Michoud Assembly Facility to go on to NASA's Stennis Space Center for further testing is an exciting leap forward in the Artemis program as NASA teams make progress toward the launch pad." The roughly 1.3-mile trip from the Michoud factory to the barge's dock is just the start of the SLS flight hardware's journey. Pegasus will ferry the SLS core stage from Michoud to Stennis, where the core stage will be lifted and placed into the historic B-2 Test Stand for the core stage Green Run test campaign that will begin later this year. The Green Run series is a comprehensive test campaign of the stage — from its avionics and propulsion systems to its four RS-25 engines — that will verify the core stage design ready for launch. "Completion of this first-time build of the Space Launch System rocket's core stages puts humans on the cusp of a new era of space exploration," said John Honeycutt, the SLS Program Manager at NASA's Marshall Space Flight Center in Huntsville, Alabama. "NASA's SLS rocket is designed to evolve so a variety of missions can be accomplished first to the Moon for the Artemis missions and then to Mars and other deep space destinations." 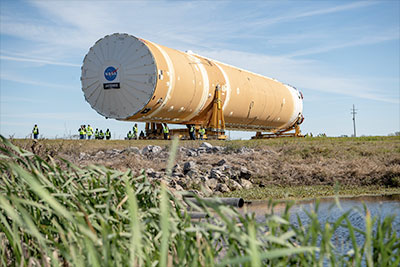 Above: NASA's Space Launch System (SLS) rocket's core stage, complete with all four RS-25 engines, is transported from NASA's Michoud Assembly Facility in New Orleans to the agency's Pegasus barge on Jan. 8. Before launching NASA's Orion spacecraft to the Moon, the SLS rocket stage will take the same water route that the first stages of the Saturn V rocket did when it was transported from Michoud to Stennis for testing during the Apollo Program in the 1960s and 1970s. Pegasus, which previously ferried the space shuttle tanks from Michoud to NASA's Kennedy Space Center in Florida, was modified to make it longer and stronger to accommodate the core stage and ferry the SLS rocket hardware. Following Green Run, the barge will carry the core stage flight hardware to Kennedy for launch preparations. The SLS rocket's core stage is the largest stage NASA has ever built at its Louisiana factory including the Saturn V rocket stages for the agency's first Moon missions. With a design featuring some of the most sophisticated hardware ever built for spaceflight, the core stage is the powerhouse of the SLS rocket. In addition to its miles of complex cabling, avionics and propulsion systems, its two propellant tanks hold a combined 733,000 gallons of propellant to power the four RS-25 engines. "This is a historic moment for NASA's Artemis program and a proud time for the Space Launch System Core Stage team as the first flight article leaves the factory floor," said Julie Bassler, the NASA SLS Stages manager. "Roll out of the core stage to Stennis ahead of the core stage Green Run test series signals an exciting next phase as NASA prepares for the first Artemis launch. The Green Run test series will verify the stage is ready to ship to the launch site.'" 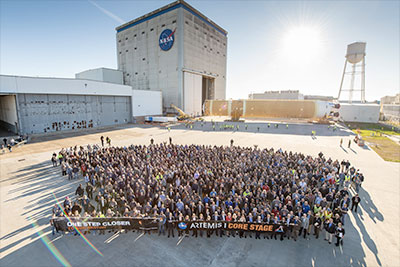 Above: NASA Deputy Administrator Jim Morhard joins Robert Champion, director of NASA's Michoud Assembly Facility in New Orleans, and John Honeycutt, SLS Program manager and NASA, Boeing and Aerojet Rocketdyne personnel in front of the fully assembled core stage for NASA's Space Launch System rocket as it rolls out from Michoud to NASA's Pegasus barge on Jan. 8. Manufacturing the SLS rocket's core stages is a combined effort for NASA and its industry partners. More than 1,100 companies across the United States contributed toward the production of the SLS rocket. Boeing built the core stage at NASA's facility in New Orleans, and Aerojet Rocketdyne upgraded and supplied the RS-25 engines. Teams at Michoud are working in tandem to manufacture and assemble core stages for the first three Artemis lunar missions. With the assembly of the core stage for Artemis I complete, NASA is focusing its efforts on building the core stages for Artemis II, the first crewed mission of SLS and NASA's Orion spacecraft, and Artemis III, the mission that will send American astronauts to the lunar South Pole. |
Robert Pearlman Editor Posts: 51606 From: Houston, TX Registered: Nov 1999
|
posted 06-15-2020 03:05 PM
collectSPACE Shuttle-flown solid rocket segments arrive in Florida for Artemis I SLS rocketA solid rocket booster segment that helped launch the Hubble Space Telescope, send the space shuttle Endeavour on its maiden mission and return John Glenn to orbit has arrived back at NASA's Florida spaceport to lift off once again — this time as part of the first Space Launch System (SLS) rocket. The steel cylinder, which will help form one of the two, five-segment motors to be mounted to the Artemis I SLS core stage, was among the hardware that was delivered by train to NASA's Kennedy Space Center on Friday (June 12). The segments' cross-country journey began seven days earlier at Northrop Grumman's facility in Promontory, Utah, where the hardware had been serviced and loaded with the solid propellant that will provide more than 75 percent of the initial thrust for the planned 2021 uncrewed launch. 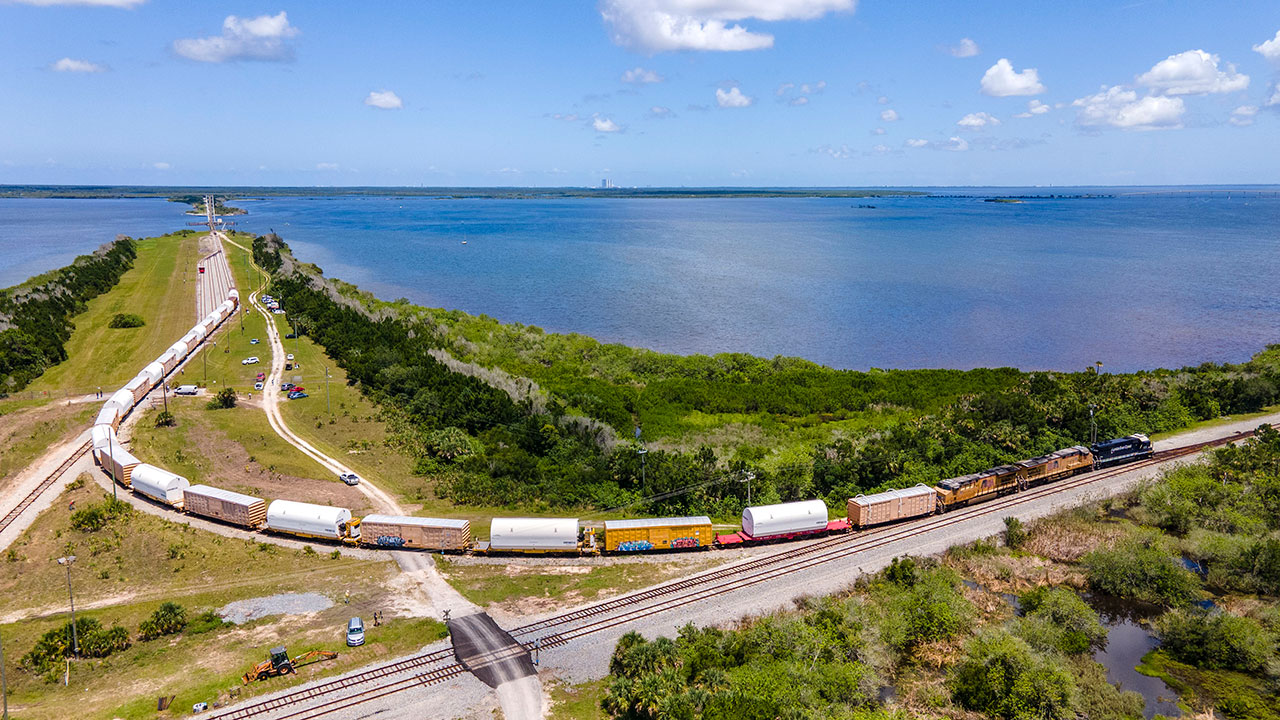 |
Robert Pearlman Editor Posts: 51606 From: Houston, TX Registered: Nov 1999
|
posted 09-01-2020 11:51 AM
NASA release Orion Program Completes Key Review for Artemis INASA's Orion Program has completed the System Acceptance Review and Design Certification Review to certify the Artemis I spacecraft is fit for flight, ready to venture from Earth to the lunar vicinity, and return home for landing and recovery. The review examined every spacecraft system, all test data, inspection reports, and analyses that support verification, to ensure every aspect of the spacecraft has the right technical maturity. In effect, the review gives the stamp of approval to the entire spacecraft development effort and is the final formal milestone to pass before integration with the Space Launch System rocket. In addition to spacecraft design, the review certified all reliability and safety analyses, production quality and configuration management systems, and operations manuals. |
Robert Pearlman Editor Posts: 51606 From: Houston, TX Registered: Nov 1999
|
posted 09-01-2020 12:03 PM
NASA photo release Orion Spacecraft Adapter (SA) Cone InstallInstallation of the spacecraft adapter (SA) cone to the Artemis I Orion spacecraft shown in progress inside the Neil Armstrong Operations and Checkout Building on Aug. 10, 2020. This is one of the final major hardware operations the spacecraft will undergo during closeout processing prior to being integrated with the Space Launch System (SLS) rocket in preparation for the first Artemis mission. The spacecraft adapter cone connects the bottom portion of Orion's service module to the top part of the rocket known as the interim cryogenic propulsion stage (ICPS). 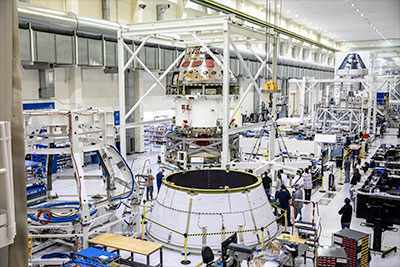 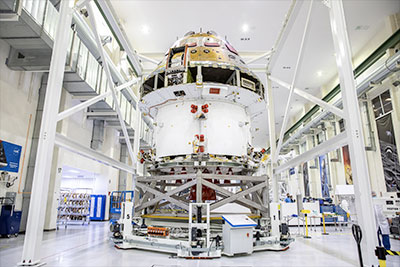
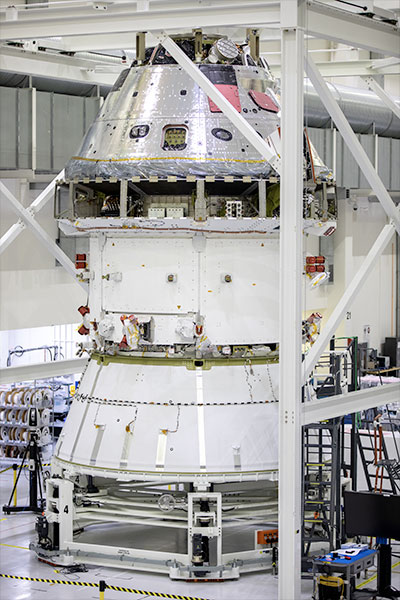
|
Robert Pearlman Editor Posts: 51606 From: Houston, TX Registered: Nov 1999
|
posted 11-27-2020 11:53 AM
NASA release Artemis I Launch Preparations Are Stacking UpNASA has stacked the first piece of the Space Launch System (SLS) rocket on the mobile launcher in preparation for the Artemis I launch next year. At NASA's Kennedy Space Center in Florida, engineers lowered the first of 10 segments into place Nov. 21 for the twin solid rocket boosters that will power the first flight of the agency's new deep space rocket. Artemis I will be an uncrewed flight to test the SLS rocket and Orion spacecraft as an integrated system ahead of crewed flights to the Moon with the Artemis program. 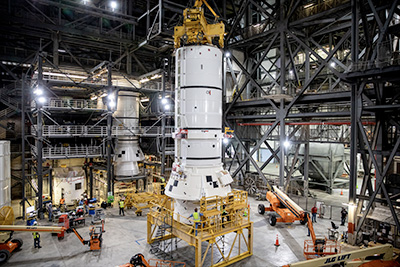 Above: The solid rocket boosters are the first components of the SLS rocket to be stacked and will help support the remaining rocket pieces and the Orion spacecraft. (NASA/Kim Shiflett) The booster segments arrived by train at the Florida spaceport in June from Northrop Grumman's manufacturing facility in Utah to undergo final launch preparations. Stacking operations began Nov. 19 with engineers transporting a booster segment from the Rotation, Processing and Surge Facility to the 525-foot-tall Vehicle Assembly Building (VAB). Each booster consists of five segments and will provide 7 million pounds of thrust for the liftoff from Launch Pad 39B. When assembled, each booster will be about half the length of a football field, and together they will generate more thrust than 14 four-engine jumbo commercial airliners. Once stacked, the SLS rocket will stand taller than the Statue of Liberty and have about 15% more thrust at liftoff than the Apollo program Saturn V rocket, making it the most powerful rocket ever built. 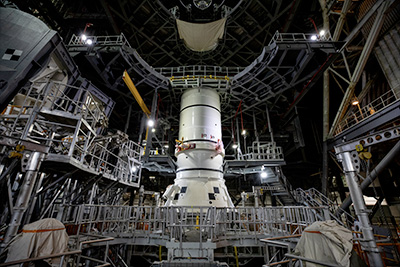 Above: The aft segments of the Space Launch System solid rocket boosters for the Artemis I mission prepare to move from high bay 4 inside the Vehicle Assembly Building for stacking on the mobile launcher inside high bay 3 at Kennedy Space Center in Florida. (NASA/Cory Huston) "Stacking the first piece of the SLS rocket on the mobile launcher marks a major milestone for the Artemis Program," said Andrew Shroble, an integrated operations flow manager with Jacobs. "It shows the mission is truly taking shape and will soon head to the launch pad." The solid rocket boosters are the first components of the SLS rocket to be stacked and will help support the remaining rocket pieces and the Orion spacecraft. Over the next several weeks, workers will use an overhead crane that can hold up to 325 tons (the weight of about 50 elephants), to lift the remaining segments one by one and place them carefully onto the 380-foot-tall mobile launcher, the structure used to process, assemble, and launch the SLS rocket. The cranes are precise enough to lower an object onto an egg without cracking it. The first booster segments to be stacked are the bottom sections known as the aft assemblies. These house the system that controls 70% of the steering during initial ascent of the rocket. This section includes the aft motor segment and skirt, and the nozzle that directs the hot gas leaving the motor. After stacking the other four segments, the final pieces of the boosters are the forward assemblies, which include the nose cone that serves as the aerodynamic leading edge of the boosters. The forward assemblies will attach to the core stage when it arrives next year. 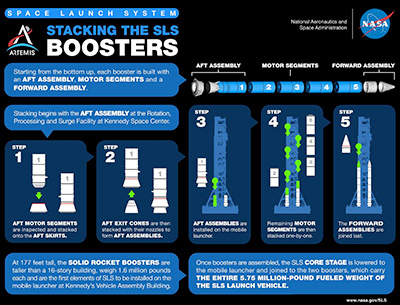 |
Robert Pearlman Editor Posts: 51606 From: Houston, TX Registered: Nov 1999
|
posted 11-30-2020 11:00 PM
NASA update Update on Orion Final Assembly and TransferNASA's Orion spacecraft for the Artemis I mission is completing final assembly at the agency's Kennedy Space Center in Florida. Engineers recently installed the three spacecraft jettison fairing panels to protect the European Service Module and the forward bay cover, which protects the upper part of Orion including its parachutes throughout its mission. While powering up the spacecraft to prepare for the pressurization of the crew module uprighting system, which ensures the capsule is oriented upward after splashdown, engineers identified an issue with a redundant channel in a power and data unit (PDU) on Orion's crew module adapter. The team is continuing with other closeout activities while troubleshooting the issue, including installation of temporary covers to ensure components are protected during ground processing and fit checks for bonded tile on the crew module side hatch. Following a resolution of the issue, NASA will transfer Orion from the Neil Armstrong Operations and Checkout Building to the Multi-Payload Processing Facility where the spacecraft will undergo fueling ahead of stacking with the launch abort system. |
Robert Pearlman Editor Posts: 51606 From: Houston, TX Registered: Nov 1999
|
posted 12-17-2020 08:23 PM
NASA release Artemis I Orion Progress UpdateDuring final assembly of the Orion spacecraft at Kennedy Space Center in Florida, engineers identified an issue with a redundant channel on one of the spacecraft's Power and Data Unit (PDU) communication cards. Orion has a total of eight PDUs, each of which has two cards with two redundant channels on each card that help provide communication between Orion's flight computers to its components. As a spacecraft designed to carry humans to deep space, Orion is built with significantly more redundancy to protect against failures than a robotic spacecraft. The PDU is still fully functional and will use its primary channel during the Artemis I mission, which is a non-crewed test flight. During their troubleshooting, engineers evaluated the option to "use as is" with the high-degree of available redundancy or remove and replace the box. They determined that due to the limited accessibility to this particular box, the degree of intrusiveness to the overall spacecraft systems, and other factors, the risk of collateral damage outweighed the risk associated with the loss of one leg of redundancy in a highly redundant system. Therefore, NASA has made the decision to proceed with vehicle processing. NASA has confidence in the health of the overall power and data system, which has been through thousands of hours of powered operations and testing. Engineers will perform additional testing and continue to monitor the health of the spacecraft while Orion is powered on to provide continued confidence in the system. NASA will proceed with spacecraft processing, and engineers are currently completing final closeout activities and will transfer the spacecraft in mid-January from the Neil Armstrong Operations and Checkout Facility to the Multi-Payload Processing Facility for fueling and preparation for integration with the Space Launch System rocket. The new timeline does not impact the launch schedule, and NASA remains on track for a launch in November 2021. |
Robert Pearlman Editor Posts: 51606 From: Houston, TX Registered: Nov 1999
|
posted 02-23-2021 03:58 PM
NASA release NASA 'Meatball' Insignia and ESA Logo Added to Artemis I FairingsNASA’s Artemis I Orion spacecraft is being outfitted with additional artwork as technicians began installing the logo for ESA (European Space Agency). ESA provided the European-built service module, which provides power and propulsion for the Orion spacecraft, and will also provide water and air for astronauts on future missions. Artemis I extends NASA and ESA’s strong international partnership beyond low-Earth orbit to lunar exploration with Orion on Artemis missions. The ESA logo joins the historic NASA “meatball” insignia on the Artemis I spacecraft adapter jettison fairing panels that protect the service module during launch. Orion is currently stationed at NASA’s Kennedy Space Center in the Multi-Payload Processing Facility, where it will undergo fueling and servicing by NASA’s Exploration Ground Systems and Jacobs Technology teams in preparation for the upcoming flight test with the Space Launch System rocket under the agency’s Artemis program. 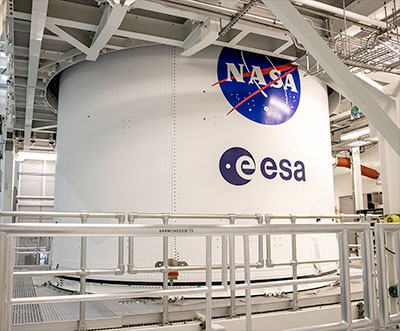 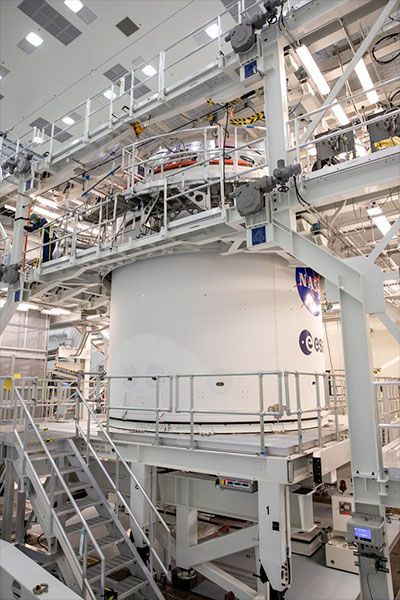
|
Robert Pearlman Editor Posts: 51606 From: Houston, TX Registered: Nov 1999
|
posted 03-11-2021 09:32 AM
NASA release Artemis I Rocket Boosters Stacked on Mobile LauncherStacking is complete for the twin Space Launch System (SLS) solid rocket boosters for NASA's Artemis I mission. 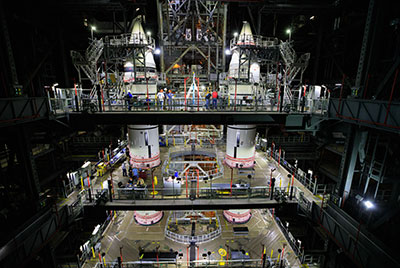 Above: The Space Launch System twin solid rocket boosters are fully assembled and stacked on the mobile launcher inside the Vehicle Assembly Building at NASA's Kennedy Space Center in Florida on March 3, 2021. (NASA/Isaac Watson) Over several weeks, workers used one of five massive cranes to place 10 booster segments and nose assemblies on the mobile launcher inside the Vehicle Assembly Building (VAB) at NASA's Kennedy Space Center in Florida. Engineers with Exploration Ground Systems placed the first segment on Nov. 21, 2020, and continued the process until the final nose assembly was placed on March 2. Prior to the arrival of the core stage, the team will finish installing electrical instrumentation and pyrotechnics, then test the systems on the boosters. When the SLS core stage arrives at Kennedy, technicians will transport it to the VAB and then stack it on the mobile launcher between the two boosters. The SLS will be the most powerful rocket in the world, producing up to 8.8 million pounds of thrust during its Artemis I launch. 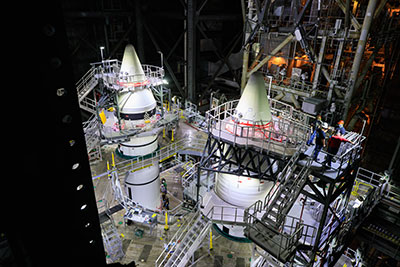 "Seeing the Space Launch System solid rocket boosters stacked completely on the Mobile Launcher for the first time makes me proud of the entire team especially the Exploration Ground Systems crew at Kennedy who are assembling them and also the teams at Marshall and Northrop Grumman who designed, tested and built them," said Bruce Tiller, the SLS boosters manager at NASA's Marshall Space Flight Center. "This team has created the tallest, most powerful boosters ever built for flight, boosters that will help launch the Artemis I mission to the Moon." |
Robert Pearlman Editor Posts: 51606 From: Houston, TX Registered: Nov 1999
|
posted 04-21-2021 12:53 PM
NASA photo release NASA removes rocket core stage for Artemis moon mission from Stennis test standCrews at NASA's Stennis Space Center near Bay St. Louis, Mississippi, worked April 19-20 to remove the first flight core stage of the agency's Space Launch System rocket from the B-2 Test Stand in preparation for its transport to Kennedy Space Center in Florida. Operations required crews to lift the core stage from its vertical placement in the stand and lower it to a horizontal position on the B-2 Test Stand tarmac. The stage now will be loaded on NASA's Pegasus barge for transport to Kennedy, where it will be prepared for launch of the Artemis I mission. Removal of the largest rocket stage ever built by NASA followed completion of a series of eight Green Run tests over the past year. 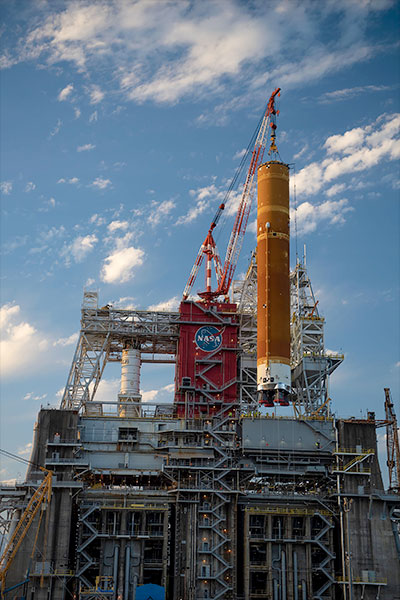 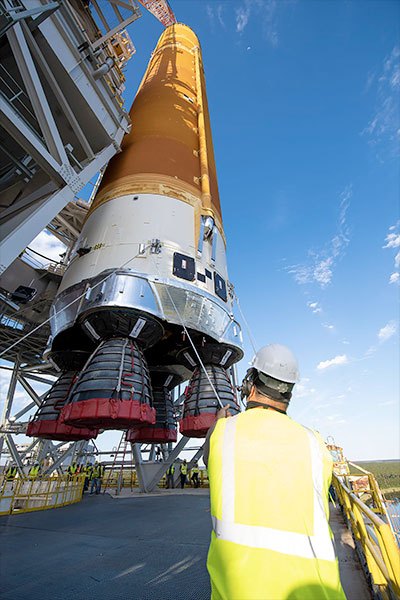
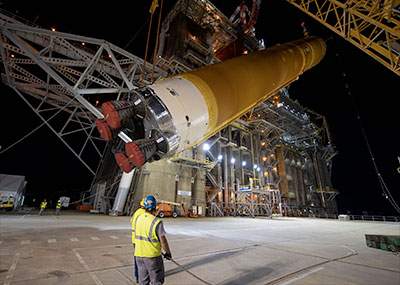
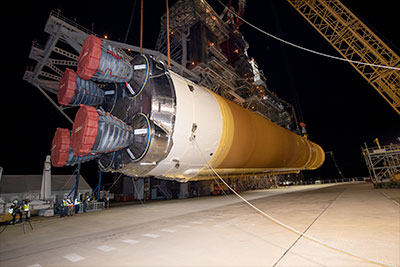
| |
Contact Us | The Source for Space History & Artifacts
Copyright 1999-2024 collectSPACE. All rights reserved.

Ultimate Bulletin Board 5.47a
|
|
|
advertisement
|